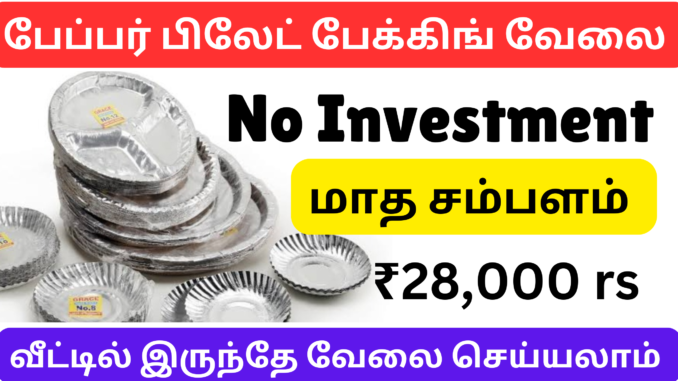
Work from home / Packing jobs at home / Earn money online tamil / How to earn online
How to make paper plate :
It sounds like you need to expand on the topic of a paper plate into a 1,000-word piece. Here are some approaches you can take:
1. Historical Background
The invention of paper plates
Who first created them and why
How they evolved over time
2. Manufacturing Process
Materials used (types of paper, coatings, recyclability)
Steps in production (cutting, pressing, shaping)
Differences between biodegradable and plastic-coated plates
3. Uses and Benefits
Everyday uses (picnics, parties, food stalls)
Convenience and hygiene benefits
How they compare to traditional plates
4. Environmental Impact
Paper plates vs. reusable plates (pros & cons)
Sustainability concerns
Recycling and disposal methods
5. Creative and DIY Projects
Art and craft ideas with paper plates
Kids’ activities (masks, clocks, decorations)
Educational uses in classrooms
6. Business and Economics
The paper plate industry
Major manufacturers and market demand
How costs affect pricing and sales
Paper Plate Manufacturing: A Comprehensive Guide
Introduction
Paper plate manufacturing is a lucrative and eco-friendly business that caters to the growing demand for disposable tableware. As consumers become increasingly aware of environmental issues, biodegradable and recyclable products like paper plates are gaining popularity. This guide provides a detailed overview of the paper plate manufacturing process, raw materials, machinery, market potential, and profitability.
Market Demand for Paper Plates
The demand for paper plates is rising due to several factors, including convenience, hygiene, and environmental concerns. They are widely used in homes, offices, restaurants, and public events. Unlike plastic plates, which take centuries to decompose, paper plates are biodegradable and eco-friendly, making them a preferred choice.
Raw Materials Required
To manufacture paper plates, the primary raw materials include:
Paperboard or Kraft Paper – The main material, available in various thicknesses and qualities.
Polyethylene (PE) Coating – Used to make the plates resistant to water and grease.
Adhesives and Starch – Needed for lamination and bonding layers.
Printing Inks (if required) – For branding and designs on plates.
Packaging Materials – Boxes and plastic wraps for storing and transporting the finished products.
Machinery and Equipment
The following machinery is required to set up a paper plate manufacturing unit:
Paper Cutting Machine – Used to cut the paper sheets into the required size.
Paper Plate Forming Machine – Converts paper into molded plate shapes using heat and pressure.
Lamination Machine – If needed, applies a thin PE layer for added strength.
Punching Machine – Shapes the plates with the required diameter.
Die and Molds – Available in different sizes and designs for various plate specifications.
Packaging Machine – Helps pack the plates efficiently for retail distribution.
Manufacturing Process
1. Paper Selection and Cutting
High-quality paper sheets or rolls are chosen based on the desired plate thickness and durability. The paper is then cut into appropriate sizes using a cutting machine.
2. Lamination (Optional)
If the plates require waterproofing, a thin PE film is laminated onto the paper sheets. This step enhances resistance to moisture and grease, making the plates suitable for serving food.
3. Die Punching and Molding
The cut paper is placed into the die-molding machine, where heat and pressure shape it into plates. Different molds create various sizes and designs, such as round, oval, or compartmentalized plates.
4. Trimming and Quality Check
After molding, the edges of the plates are trimmed to ensure uniform shape. Each batch undergoes a quality check to inspect durability, finishing, and resistance to heat and moisture.
5. Printing and Branding (If Required)
For custom designs or branding, the plates undergo a printing process where logos, patterns, or messages are imprinted using food-safe inks.
6. Stacking and Packaging
The finished plates are stacked in batches, counted, and packed into cartons or plastic covers for distribution. Proper labeling and branding ensure they meet market requirements.
Investment and Cost Analysis
The investment for setting up a small-scale paper plate manufacturing unit varies based on production capacity and automation level. Below is a rough cost breakdown:
Fixed Costs:
Machinery & Equipment – $5,000 to $50,000 (depending on automation level)
Factory Space & Rent – $500 to $2,000 per month
Licensing & Registration – $500 to $1,000
Operating Costs:
Raw Materials – $2,000 to $10,000 per month
Labor Costs – $1,500 to $5,000 per month (depending on workforce size)
Utility Bills (Electricity, Water, etc.) – $500 to $2,000 per month
Marketing & Distribution – $1,000 to $5,000 per month
Expected Revenue and Profitability:
Selling paper plates in bulk can yield substantial profits. If a unit produces 50,000 plates per day and sells at a wholesale rate of $0.05 per plate, the monthly revenue can reach $75,000. After deducting expenses, the profit margin typically ranges from 20-40%.
Legal Requirements
To operate a paper plate manufacturing business, the following legal requirements must be met:
Business Registration – Register as a sole proprietorship, partnership, or company.
GST/VAT Registration – Depending on regional tax laws.
Environmental Clearance – Necessary for waste disposal compliance.
Health & Safety Certifications – If involved in food-grade plate production.
Trade License – Obtainable from local authorities.
Marketing and Distribution Strategies
To maximize sales, businesses should employ the following marketing strategies:
Local Retail Distribution: Partner with grocery stores, supermarkets, and wholesalers.
Online Sales & E-commerce: List products on platforms like Amazon, eBay, or a dedicated website.
Corporate & Bulk Orders: Supply to event organizers, caterers, and restaurants.
Branding & Advertising: Use social media, flyers, and local advertisements to create awareness.
Eco-Friendly Positioning: Highlight biodegradability and sustainability in marketing campaigns.
Challenges in Paper Plate Manufacturing
Despite its profitability, the business has some challenges:
Raw Material Price Fluctuations – Paper and PE costs can vary, affecting profitability.
Competition – Many players in the market mean strong competition.
Machinery Maintenance – Regular servicing is necessary to avoid downtime.
Waste Management – Disposing of paper scraps in an eco-friendly way is crucial.
Regulatory Compliance – Adhering to government policies and environmental laws.
Future Prospects and Innovations
With growing environmental consciousness, the demand for biodegradable and compostable paper plates is expected to rise. Innovations such as sugarcane bagasse plates, bamboo fiber plates, and plant-based coatings are emerging trends. Additionally, automated production and AI-driven quality control are enhancing efficiency and reducing labor costs.
Conclusion
Paper plate manufacturing is a promising venture with significant market potential. By investing in quality materials, efficient machinery, and effective marketing, entrepreneurs can build a successful and sustainable business. As eco-friendly products continue to gain traction, the paper plate industry is poised for steady growth in the years to come.
Important advantages of paper plate making & packing?
Paper plate making and packing offer several important advantages, both environmentally and economically. Here are the key benefits:
Advantages of Paper Plate Making
Eco-Friendly – Paper plates are biodegradable and recyclable, making them a sustainable alternative to plastic plates.
High Demand – There is a consistent market demand for disposable plates, especially in catering, restaurants, and street food businesses.
Low Investment – Setting up a paper plate manufacturing business requires minimal capital and machinery.
Employment Generation – It creates job opportunities for both skilled and unskilled workers.
Profitability – With low raw material costs and steady demand, paper plate manufacturing can yield good profits.
Easy Availability of Raw Materials – Paperboard or Kraft paper is readily available, reducing production challenges.
Hygienic and Safe – Compared to reusable plates, paper plates reduce the risk of contamination and are widely used in hospitals, events, and public gatherings.
Advantages of Paper Plate Packing
Protects from Contamination – Proper packing prevents exposure to dust, dirt, and bacteria, ensuring hygiene.
Enhances Shelf Life – Good packaging helps maintain the shape and strength of paper plates during transport and storage.
Branding & Marketing – Custom-printed packaging with logos and labels can enhance brand recognition and attract more customers.
Easy Transportation – Well-packed plates can be transported in bulk without damage.
Eco-Friendly Packaging Options – Many paper plates come in biodegradable or recyclable packaging, further supporting environmental sustainability.
Compliance with Regulations – Proper packaging ensures adherence to hygiene and quality control standards set by authorities.
Leave a Reply