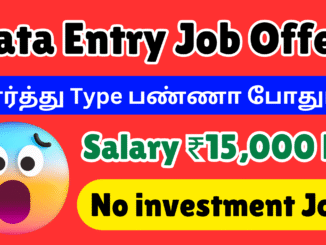
Work From Home Jobs Tamil / Home Based Jobs Tamil 2025 / Earn Money Online Tamil / Make Money Online Tamil
Work From Home Jobs Tamil / Home Based Jobs Tamil 2025 / Earn Money Online Tamil / Make Money Online Tamil How to data […]
Work From Home Jobs Tamil / Home Based Jobs Tamil 2025 / Earn Money Online Tamil / Make Money Online Tamil How to data […]
Work from home / Work from home jobs tamil / Part time jobs for students / Online jobs at home / Make money online […]
Packing jobs at home / Best packing jobs from home tamil / Work from home / Earn money online tamil Color pencil packing work […]
Work from home jobs 2025 / Part time jobs tamil / Home based jobs without investment tamil / Earn money online About customer care […]
Work from home job / Home based jobs tamil 2025 / Part time jobs for students / Earn money online tamil What is the […]
Packing jobs at home / Packing business at home / Part time jobs tamil / Work from home 2025 How to work packing jobs […]
Work From Home / Part Time Jobs tamil / Earn money online tamil / Home based jobs tamil 2025 About Unilever company job offer […]
Work from home jobs tamil / Part time jobs for students / Best part time job / Home based jobs 2025 About flipkart job […]
Work from home jobs tamil / Work from home job / Earn money online tamil / How to make money tamil Amazon Work From […]
Work From Home Jobs Tamil / Work From Home 2025 / Home Based Jobs Tamil / Part Time Jobs For Students Work from home […]
Copyright © 2025 | WordPress Theme by MH Themes