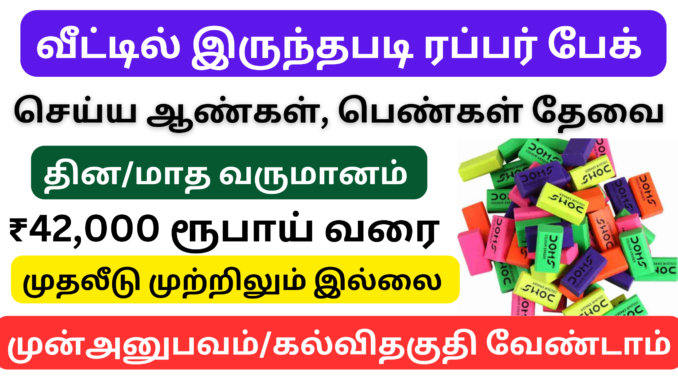
Work from home job / Part time jobs for students / Best part time job / Home based jobs without investment tamil
How to packing rubber process :
Packing rubber is a critical process in the rubber industry that involves efficiently storing and transporting rubber materials to ensure their quality and integrity. In this guide, we will explore the essential steps and considerations for packing rubber effectively in 1000 words.
Understanding Rubber Properties:
Before diving into the packing process, it’s crucial to understand the properties of rubber. Rubber is a versatile material known for its elasticity, resilience, and durability. However, it is also susceptible to damage from exposure to elements like moisture, heat, and light. Proper packing helps preserve these properties during storage and transportation.
Selecting Packaging Materials:
The choice of packaging materials is key to maintaining the quality of rubber. Common packaging materials for rubber include:
Plastic bags or polyethylene liners: These provide a barrier against moisture and contaminants.
Cardboard boxes or pallets: These offer structural support and facilitate stacking for efficient storage and transportation.
Stretch wrap or shrink wrap: These materials provide additional protection and stability to packed rubber items.
Preparation for Packing:
Before packing rubber, ensure that the rubber materials are clean, dry, and free from any contaminants. Any foreign particles or moisture can compromise the quality of the rubber during storage and transportation. Inspect the rubber for any defects or damage that may affect its integrity.
Packing Process:
The packing process typically involves the following steps:
Measuring and Weighing: Determine the quantity of rubber to be packed and weigh it accurately to ensure consistency in packaging.
Wrapping or Bagging: Place the rubber materials in appropriate packaging such as plastic bags or liners. Ensure that the packaging is sealed tightly to prevent moisture ingress.
Boxing or Palletizing: If packing in boxes or on pallets, arrange the wrapped rubber materials securely to prevent shifting or damage during handling and transportation.
Securing: Use stretch wrap or shrink wrap to secure the boxes or pallets, providing additional protection and stability.
Labeling and Documentation:
Proper labeling is essential for easy identification and tracking of packed rubber materials. Each package should be labeled with relevant information such as:
Product description
Quantity
Date of packing
Handling instructions (if any)
Hazardous material warnings (if applicable)
Quality Control:
Implement quality control measures throughout the packing process to ensure that packed rubber materials meet the required standards. This may include visual inspections, random sampling, and quality assurance checks to detect any defects or irregularities.
Storage Considerations:
Proper storage is crucial for maintaining the quality of packed rubber materials. Store the packed rubber in a clean, dry, and well-ventilated area away from direct sunlight, heat sources, and moisture. Ensure that the storage area is free from pests and other contaminants that may damage the rubber.
Transportation and Handling:
When transporting packed rubber materials, handle them with care to prevent damage or mishandling. Use appropriate lifting and handling equipment to avoid strain or injury. Secure the packed materials properly during transit to minimize the risk of shifting or damage.
Environmental Considerations:
Consider environmental factors when packing rubber, especially if it is being transported over long distances or stored for extended periods. Extreme temperatures, humidity, and exposure to sunlight can degrade the quality of rubber. Choose packaging materials and storage conditions that provide adequate protection against these environmental factors.
Regulatory Compliance:
Ensure compliance with relevant regulations and standards governing the packing, storage, and transportation of rubber materials. This includes adhering to safety regulations, hazardous material handling guidelines, and any specific requirements for shipping rubber products.
Documentation and Record-Keeping:
Maintain detailed records of the packing process, including packing dates, quantities packed, packaging materials used, and any quality control checks performed. This documentation is essential for traceability, quality assurance, and regulatory compliance.
Continuous Improvement:
Regularly review and evaluate the packing process to identify areas for improvement. Solicit feedback from employees involved in the packing process and implement changes to enhance efficiency, reduce waste, and improve the quality of packed rubber materials.
In conclusion, effective packing of rubber materials is crucial for preserving their quality, integrity, and performance throughout storage and transportation.
By following the steps outlined in this guide and paying attention to key considerations such as packaging materials, quality control, storage, and transportation, you can ensure that your packed rubber materials meet the required standards and arrive at their destination safely and in optimal condition.
What is the procedure of rubber making?
Rubber production involves several steps, primarily for natural rubber, which is obtained from the latex of the rubber tree. Here’s an overview:
Harvesting: Latex, the milky substance containing rubber particles, is collected from rubber trees. This process involves making incisions in the bark of the tree and collecting the latex in containers.
Coagulation: The collected latex is then treated to coagulate the rubber particles. This can be done by adding acid or by using a coagulant like formic acid or calcium nitrate. Coagulation causes the rubber particles to come together and separate from the liquid.
Forming: The coagulated rubber is then formed into sheets or blocks. This can be done manually or using machines. The formed rubber is then washed to remove impurities.
Milling: The rubber sheets or blocks are passed through mills to further refine and homogenize them. This process helps to break down any remaining lumps and improve the quality of the rubber.
Vulcanization: Vulcanization is a chemical process that involves heating the rubber with sulfur and other additives. This process cross-links the rubber molecules, making the material more durable, elastic, and resistant to heat and chemicals. Vulcanization is crucial for giving rubber its desirable properties.
Finishing: After vulcanization, the rubber is shaped into its final form through processes like molding, extrusion, or calendaring. It may also undergo additional treatments such as washing, drying, and finishing to enhance its appearance and properties.
Quality Control: Throughout the production process, quality control measures are implemented to ensure that the rubber meets the desired specifications and standards. This includes testing for strength, elasticity, durability, and other properties.
These steps outline the general procedure for natural rubber production. Synthetic rubber production follows a different process, typically involving the polymerization of petroleum-derived monomers.
List of ingredients used in rubber making?
Rubber can be made from either natural sources or synthetic materials. Here’s a list of ingredients commonly used in both natural and synthetic rubber manufacturing:
Natural rubber latex: The primary ingredient in natural rubber production, obtained from the latex sap of certain trees, especially the Hevea brasiliensis tree.
Synthetic rubber polymers: Various synthetic polymers can be used, such as styrene-butadiene rubber (SBR), polybutadiene rubber (BR), polyisoprene rubber (IR), and ethylene-propylene-diene monomer (EPDM).
Fillers: Substances like carbon black, silica, clay, and calcium carbonate are added to improve the mechanical properties and reduce costs.
Vulcanizing agents: Compounds such as sulfur or peroxides are used to cross-link the polymer chains, increasing the rubber’s strength, elasticity, and durability.
Accelerators: Chemicals like zinc oxide and accelerators such as thiurams, mercaptobenzothiazoles, and dithiocarbamates are added to speed up the vulcanization process.
Antioxidants: Prevent degradation of the rubber due to exposure to oxygen and heat. Examples include phenols and amines.
Plasticizers: These are used to improve flexibility and reduce stiffness. Oils and resins are common plasticizers.
Softeners: Materials like pine tar or petroleum resins can be added to adjust the hardness or tackiness of the rubber.
Activators: Substances like zinc oxide are used to enhance the effectiveness of accelerators.
Antiozonants: Protect the rubber from degradation caused by exposure to ozone, which can lead to cracking. Examples include waxes and chemicals like paraphenylene diamine (PPD).
Stabilizers: Compounds added to prevent degradation of the rubber due to exposure to light or heat.
Flame retardants: These are added to make rubber products less flammable, commonly used in applications where fire safety is critical.
Colorants: Dyes or pigments may be added to give the rubber a specific color.
Processing aids: Substances like fatty acids or metal oxides are added to improve processing characteristics such as flow and mold release.
The specific formulation of rubber may vary depending on the intended application and desired properties of the final product.
Advantage & disadvantages of rubber packing?
Rubber packing, also known as rubber seals or gaskets, are commonly used in various industries for sealing purposes due to their flexibility, durability, and resistance to various environmental conditions. Here are some advantages and disadvantages of using rubber packing:
Advantages:
Sealing properties: Rubber packing effectively seals gaps, preventing leaks of liquids or gases. It provides a tight seal even in irregular or rough surfaces, reducing the risk of leakage.
Flexibility: Rubber packing is flexible and can conform to different shapes and sizes, making it suitable for sealing applications in a wide range of equipment and machinery.
Chemical resistance: Many rubber compounds exhibit excellent resistance to a wide range of chemicals, including oils, fuels, acids, and bases. This makes rubber packing suitable for use in environments where exposure to various chemicals is a concern.
Temperature resistance: Rubber packing can withstand a wide range of temperatures, from extreme cold to high heat, without losing its sealing properties. This makes it suitable for use in both indoor and outdoor applications.
Shock absorption: Rubber packing can act as a cushion, absorbing shocks and vibrations in machinery, which helps reduce wear and tear on equipment and prolongs its lifespan.
Disadvantages:
Degradation: Rubber packing may degrade over time due to exposure to UV radiation, ozone, heat, and other environmental factors. This can lead to a loss of sealing effectiveness and the need for frequent replacement.
Compatibility: Not all rubber compounds are compatible with every type of fluid or gas they may come into contact with. Using the wrong type of rubber packing in a particular application can lead to chemical reactions, degradation, and failure of the seal.
Cost: In some cases, rubber packing can be more expensive than other sealing materials, particularly for specialized compounds or custom designs. This can increase the overall cost of equipment or maintenance.
Compression set: Rubber packing may experience compression set over time, especially when subjected to prolonged compression or high temperatures. This can cause the seal to lose its elasticity and sealing effectiveness.
Installation complexity: Installing rubber packing correctly requires careful attention to detail to ensure a proper seal. Improper installation can lead to leaks or premature failure of the seal.
Despite these disadvantages, rubber packing remains a popular choice for sealing applications in many industries due to its versatility, effectiveness, and durability. Proper selection, installation, and maintenance can help mitigate these drawbacks and maximize the performance of rubber packing seals.
Leave a Reply