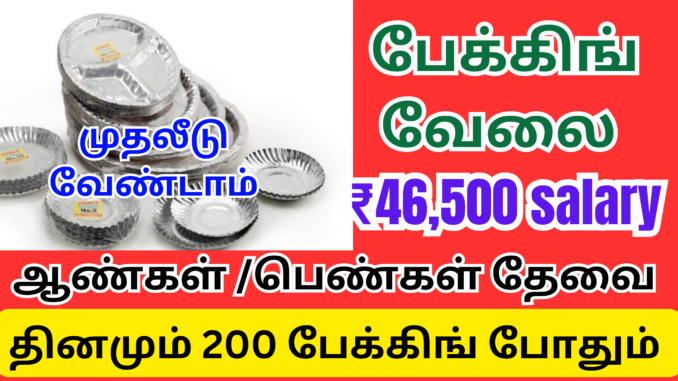
Work from home / Earn money online tamil / Packing jobs at home / Packing jobs from home
Paper cup making process :
Certainly! Here’s an overview of the paper cup making process:
The Paper Cup Making Process
Paper cups are ubiquitous in modern life, providing a convenient solution for drinking beverages on the go. The manufacturing process of these cups is intricate, involving several stages to ensure quality, functionality, and environmental sustainability. Below is a detailed breakdown of the paper cup making process.
1. Raw Material Preparation
The primary raw materials for paper cup production are paper and polyethylene. The paper used is usually a type of food-grade paper that is coated with a thin layer of polyethylene. The paper is typically made from a combination of virgin and recycled fibers, ensuring strength and durability.
Paper Production: Paper is produced by pulping wood fibers, which are then mixed with water to form a slurry. This slurry is spread onto large screens to form paper sheets. The sheets are dried and pressed to create the final paper rolls used in cup production.
Polyethylene Coating: Polyethylene is applied to one side of the paper to make it water-resistant and to prevent leaks. This coating process involves extruding molten polyethylene onto the paper, which is then cooled and solidified. This coating is crucial for ensuring that the paper cup can hold liquids without disintegrating.
2. Printing and Cutting
Once the paper rolls are coated and ready, they are fed into printing machines. Here, the design and branding are printed onto the paper. The printing process can involve various techniques such as flexographic or offset printing, depending on the complexity and quality of the design.
Flexographic Printing: This method uses flexible relief plates to transfer ink onto the paper. It is suitable for high-speed production and is often used for printing simple designs.
Offset Printing: Offset printing involves transferring ink from a plate to a rubber blanket and then onto the paper. This method provides higher quality and is used for more detailed or multi-color designs.
After printing, the large rolls of paper are cut into smaller sheets or blanks that are sized appropriately for forming the cups.
3. Forming the Cup
The next stage is the actual formation of the paper cups. This involves several sub-processes:
1. Cup Blanking: In this step, the printed paper is cut into circular blanks, which are the basic shapes used to form the body of the cup. The size and shape of the blank depend on the intended cup size and design.
2. Cup Forming: The circular paper blanks are fed into a cup forming machine. This machine heats and shapes the paper blanks into the cup’s body. The process involves several steps:
Heating: The paper is heated to make it more pliable.
Molding: The heated paper is then molded into a cup shape using a series of dies and molds.
Sealing: The edges of the cup are sealed together using a combination of heat and pressure. This creates a strong, leak-proof seam.
3. Bottom Insertion: After the cup body is formed, a paper or plastic bottom is inserted and sealed into place. This bottom piece is usually pre-cut to the correct size and shape and is sealed using a similar heat-sealing process.
4. Quality Control and Inspection
Quality control is a critical part of the paper cup manufacturing process. Each cup is inspected for defects, such as leaks, improper sealing, or misprints. Quality control measures ensure that the cups meet safety standards and are free from any issues that might affect their performance or appearance.
Testing for Leakage: Cups are tested for leakage by filling them with water and checking for any signs of seepage. This ensures that the polyethylene coating is effectively preventing leaks.
Strength and Durability Testing: The cups are also tested for structural integrity to ensure they can hold the intended amount of liquid without collapsing or deforming.
5. Packaging and Distribution
Once the cups pass inspection, they are packed into cartons or boxes for distribution. The packaging process involves counting the cups, placing them into containers, and labeling them for shipping. Proper packaging is essential to prevent damage during transportation and handling.
Storage: The packed cups are stored in a warehouse until they are needed. Proper storage conditions are maintained to ensure that the cups remain in good condition.
Distribution: The cups are then distributed to retailers, food service providers, or other customers. Efficient logistics and distribution channels are essential to ensure that the cups reach their destination in a timely manner.
6. Environmental Considerations
As environmental concerns continue to grow, the paper cup industry has been making efforts to become more sustainable. Some key considerations include:
1. Recycled Materials: Increasing the use of recycled paper and materials helps reduce the environmental impact of paper cup production.
2. Compostable and Biodegradable Options: Innovations in biodegradable coatings and materials are being explored to make paper cups more eco-friendly.
3. Recycling Programs: Encouraging recycling and proper disposal of paper cups helps minimize waste and promote environmental sustainability.
The process of making paper cups involves a combination of paper preparation, printing, cup forming, quality control, and distribution. Each stage is carefully managed to ensure that the final product is functional, durable, and meets quality standards. As the industry evolves, ongoing advancements in materials and processes aim to address environmental concerns and improve the sustainability of paper cup production.
How to making paper cups :
How to Make Paper Cups: A Comprehensive Guide
Introduction
Paper cups are a ubiquitous item, found in nearly every foodservice setting, from coffee shops to fast food joints. Their convenience, combined with their relatively low cost, makes them a popular choice for serving beverages. But have you ever wondered how these seemingly simple items are made? This guide will take you through the process of creating paper cups from start to finish, detailing the materials, machinery, and steps involved.
Materials and Equipment
Paper: The primary material used in making paper cups is a special type of paper known as cup stock. This is typically a coated paperboard that includes a layer of polyethylene (PE) or another polymer to make it water-resistant. The paper is designed to hold liquids without becoming soggy.
Coating: To ensure the cup can hold liquids without leaking, the paper is coated with a layer of plastic or wax. This coating provides a barrier that prevents the liquid from seeping through the paper.
Printing Ink: For branded or decorative cups, printing ink is used to add logos, designs, or other information.
Cup Forming Machinery: Specialized machines are required to cut, form, and seal the paper into cup shapes. These machines are often capable of high-speed production and can handle large volumes.
Cutting Dies and Punches: These are used to cut and shape the paperboard into the appropriate patterns and sizes for the cups.
The Manufacturing Process
Paper Preparation
The process begins with large rolls of paperboard, which are unrolled and fed into a machine that applies the plastic or wax coating. This coating process involves heating and applying the coating material to the paperboard to ensure it is evenly distributed and properly adhered. Once coated, the paperboard is cooled and wound onto large rolls for further processing.
Printing (Optional)
If the paper cups are to feature designs or branding, the next step is printing. This is done using either flexographic printing or offset printing, depending on the quality and type of design. The paperboard is fed into a printing press where the desired designs are applied. The ink must be allowed to dry completely before the paperboard can be used for cup forming.
Cutting and Shaping
The coated (and possibly printed) paperboard is then fed into a die-cutting machine. This machine uses cutting dies and punches to cut the paperboard into specific shapes and sizes. The shapes include the cup’s body and the rim. This stage involves precision cutting to ensure that all the pieces fit together correctly during the forming stage.
Cup Forming
The cut paperboard pieces are then fed into a cup-forming machine. This machine takes the flat, cut pieces and forms them into cup shapes. The process involves several key steps:
Cupping: The machine wraps the paperboard around a cup-shaped mold, forming the basic cup shape.
Heat Sealing: The edges of the paperboard are sealed together using heat and pressure. This is usually done at the rim and base of the cup. The heat melts the plastic coating, which then solidifies and bonds the edges together.
Rim Forming: The rim of the cup is folded and crimped to create a sturdy lip. This step is crucial for ensuring that the cup can hold a lid securely if needed.
Quality Control
After forming, the cups undergo a quality control inspection to ensure they meet the required standards. This involves checking for leaks, ensuring the rims are properly formed, and verifying that the cups are free of defects. Some manufacturers use automated inspection systems, while others rely on manual checks.
Packing and Distribution
Once the cups pass inspection, they are stacked and packed into cartons. These cartons are then labeled and prepared for distribution. The packing process is designed to protect the cups during transportation and ensure they reach their destination in good condition.
Environmental Considerations
Making paper cups involves several environmental considerations. The production process uses resources and generates waste, so many manufacturers are working towards more sustainable practices. This includes using recycled paper, reducing plastic use, and developing biodegradable or compostable coatings.
Innovations in Paper Cup Technology
Recent advancements in paper cup technology have focused on improving sustainability. Innovations include:
Biodegradable Coatings: New types of coatings made from natural materials are being developed to replace traditional plastic coatings. These coatings break down more easily in the environment.
Recycling Programs: Some companies are implementing take-back programs where used cups can be collected, cleaned, and recycled into new paper products.
Reduced Plastic Use: Research is ongoing into reducing the amount of plastic used in the coatings, or finding alternatives that are less harmful to the environment.
Making paper cups is a multifaceted process that combines materials science with precise manufacturing techniques. From the preparation of coated paperboard to the high-speed forming and quality control, each step is crucial in producing a functional and reliable product. While traditional paper cups involve some environmental impact, ongoing innovations are aimed at reducing this impact and improving sustainability. Understanding the process behind these everyday items can give us a greater appreciation for the technology and effort involved in their production.
Leave a Reply