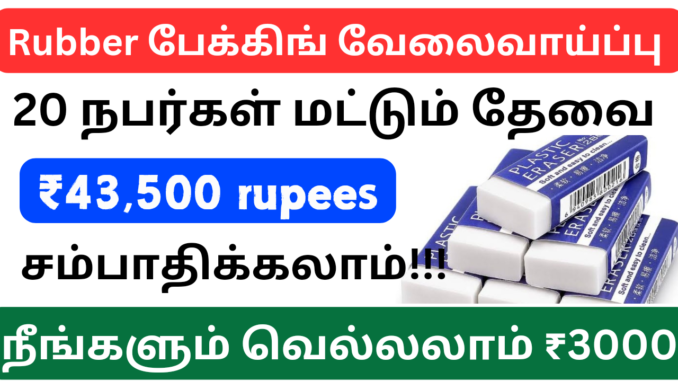
Packing jobs tamil 2024 / Packing business at home / Packing jobs at home / Work from home
Eraser making methods :
Here’s a detailed overview of various methods for making erasers, exploring different materials, techniques, and historical context.
Introduction
Erasers are essential tools for anyone who writes, draws, or sketches. Their primary function is to remove pencil marks from paper, but they come in various shapes, sizes, and materials. This article will delve into the methods of making erasers, examining traditional rubber-based processes, modern synthetic methods, and innovative alternatives.
Historical Context
The first erasers were made from natural materials such as bread. In the 1770s, a man named Edward Naime is credited with creating the first commercial rubber eraser, using the rubber tree’s latex. The popularity of rubber erasers surged in the 19th century with the advent of mass production techniques. Today, we have a wide range of erasers, from traditional rubber types to synthetic varieties.
Materials Used in Eraser Production
Natural Rubber:
Derived from the latex of rubber trees.
Provides good flexibility and a soft touch, making it effective at lifting graphite from paper.
Synthetic Rubber:
Created through polymerization processes.
Common types include styrene-butadiene rubber (SBR) and thermoplastic elastomers (TPE), which can be tailored for specific properties.
PVC (Polyvinyl Chloride):
Used for its durability and flexibility.
Often found in colored erasers and those with unique designs.
Thermoplastic Elastomers:
A blend of rubber and plastic, these materials can be molded and reshaped.
They offer various hardness levels and colors, making them suitable for a wide range of eraser designs.
Alternative Materials:
Some modern erasers incorporate materials like recycled rubber, foam, or even biodegradable substances to appeal to eco-conscious consumers.
Traditional Rubber Eraser Manufacturing Process
Material Preparation:
Raw rubber is collected from rubber trees and processed to remove impurities.
This involves washing, drying, and grinding the latex.
Compounding:
The processed rubber is mixed with additives such as fillers (to improve texture), plasticizers (to enhance flexibility), and stabilizers (to prolong shelf life).
Common fillers include clay and calcium carbonate, which provide bulk and modify the eraser’s hardness.
Molding:
The compounded rubber mixture is poured into molds to create the desired shapes (pencil-top, block, etc.).
Molds can be made from metal or silicone, allowing for intricate designs.
Curing:
The molds are placed in a curing oven to vulcanize the rubber, which involves heating the material to cross-link the polymers, enhancing strength and elasticity.
This process can take several hours, depending on the thickness and type of rubber used.
Finishing:
After curing, the erasers are removed from the molds and trimmed to ensure uniformity.
Additional finishing processes may include sanding, polishing, or printing logos and designs.
Synthetic Eraser Manufacturing Process
Polymerization:
Synthetic rubbers are produced through chemical reactions that create polymers from monomers, such as butadiene and styrene.
Different ratios and catalysts can create various properties, influencing hardness and elasticity.
Compounding and Molding:
Similar to traditional methods, the synthetic rubber is mixed with fillers and additives.
The mixture is then molded into shape using either injection molding or extrusion processes.
Cooling and Curing:
Unlike natural rubber, synthetic erasers might not require a curing process unless specific properties are desired.
They can be cooled rapidly, reducing production time.
Finishing:
Synthetic erasers undergo finishing processes similar to those of natural rubber, including trimming and surface treatments.
Innovative Methods and Future Directions
Recycled Materials:
With increasing environmental awareness, some manufacturers are producing erasers from recycled rubber or other waste materials.
These methods not only reduce waste but also appeal to eco-conscious consumers.
Biodegradable Erasers:
Researchers are exploring plant-based alternatives that can decompose naturally.
These erasers use materials such as cornstarch or other biodegradable polymers.
3D Printing:
The advent of 3D printing technology allows for customizable erasers.
Consumers can design their own shapes and sizes, tailoring erasers to their specific needs.
Enhanced Performance:
Some manufacturers are experimenting with erasers that include special properties, such as dual-function erasers (for both graphite and ink) or those with built-in sharpeners.
The methods of making erasers have evolved significantly over the years, transitioning from simple natural materials to complex synthetic processes. Whether using traditional rubber or modern alternatives, the goal remains the same: to provide an effective tool for correcting mistakes.
As technology and environmental awareness continue to advance, the future of eraser production promises exciting innovations that cater to diverse consumer needs while minimizing environmental impact. Whether you prefer the classic rubber eraser or a high-tech, eco-friendly alternative, the evolution of erasers showcases the blend of practicality and creativity in our everyday tools
Eraser packing process :
Here’s a detailed overview of the eraser packing process, broken down into sections to provide a comprehensive understanding.
Introduction to Eraser Manufacturing
Erasers are essential stationery items, widely used in schools, offices, and homes. The production of erasers involves several stages, from material selection to packaging. This overview focuses specifically on the packing process, which is crucial for ensuring product integrity and customer satisfaction.
Materials Used in Eraser Production
Erasers are typically made from materials like PVC (polyvinyl chloride), TPR (thermoplastic rubber), or latex. These materials offer the right balance of softness and durability, allowing for effective erasing without damaging paper. Once manufactured, these erasers need to be packed carefully to maintain quality.
The Packing Process
Quality Control Before Packing
Before packing, finished erasers undergo a quality control inspection. This ensures that they meet standards for size, color, texture, and functionality. Any defective products are discarded or recycled, preventing them from reaching the consumer.
Preparing for Packing
After quality control, the erasers are sorted based on type, color, and size. This step is essential for efficient packing and inventory management. Workers or automated systems may perform sorting, depending on the scale of production.
Selection of Packaging Materials
The choice of packaging materials is critical. Common options include:
Plastic Bags: Lightweight and clear, allowing visibility of the product.
Boxes: Sturdy and stackable, suitable for retail display.
Blister Packs: Offer additional protection and an appealing presentation.
Shrink Wrap: Often used for bulk erasers, providing a tight seal.
The choice depends on the target market and distribution method.
Packing Configuration
The configuration of erasers in the packaging is crucial for both protection and presentation. Common configurations include:
Single Packs: Ideal for retail settings where consumers can purchase one eraser at a time.
Multi-Packs: Grouping several erasers together, often with variations in color or type, to encourage bulk purchases.
Bulk Packaging: Used for wholesale distribution, where large quantities are packed together.
Automated Packing Systems
Many modern factories use automated packing machines to increase efficiency. These systems can:
Fill: Automatically dispense a set number of erasers into bags or boxes.
Seal: Ensure that each package is securely closed to prevent contamination.
Label: Apply labels with product information, barcodes, and branding.
Automation reduces labor costs and increases packing speed, but human oversight is still important to monitor for errors.
Manual Packing Procedures
In smaller operations or for specialty products, manual packing might be preferred. This involves workers:
Filling Packages: Carefully placing erasers into bags or boxes.
Sealing Packages: Using heat sealers or tape to secure packages.
Labeling: Manually applying labels to ensure accuracy.
Manual packing allows for more customization and attention to detail, particularly for unique or limited-edition products.
Packaging and Storage Considerations
Proper packing also involves consideration of how the products will be stored and transported. Factors include:
Protection from Damage: Using cushioning materials or dividers within boxes to prevent crushing.
Moisture Resistance: Ensuring packaging materials are suitable for varying humidity levels.
Weight Distribution: Packing heavier items at the bottom to maintain stability during transport.
Final Quality Assurance
Once packed, a final quality assurance check is performed. This step verifies that:
The correct number of items is in each package.
The packages are sealed properly.
Labels are legible and correctly positioned.
Any discrepancies are corrected before the products move to the next stage.
Distribution of Packaged Erasers
After packing, erasers are prepared for distribution. This involves:
Inventory Management:
Keeping track of packed erasers helps in planning future production and managing supply chain logistics.
Transportation:
Products are loaded onto trucks or shipping containers for distribution. Considerations during this stage include:
Temperature Control: Ensuring that the transportation conditions do not affect the integrity of the erasers.
Timely Delivery: Coordinating with logistics teams to meet delivery deadlines.
Conclusion
The packing process for erasers is a critical step in the production cycle, ensuring that products reach consumers in optimal condition. From initial quality checks to final distribution, each stage plays a vital role in maintaining product integrity and meeting customer expectations.
As technology advances, the packing process continues to evolve, incorporating more automation and efficiency while still valuing the importance of quality assurance. Ultimately, effective packing not only preserves the product but also enhances brand reputation and consumer satisfaction.
Leave a Reply