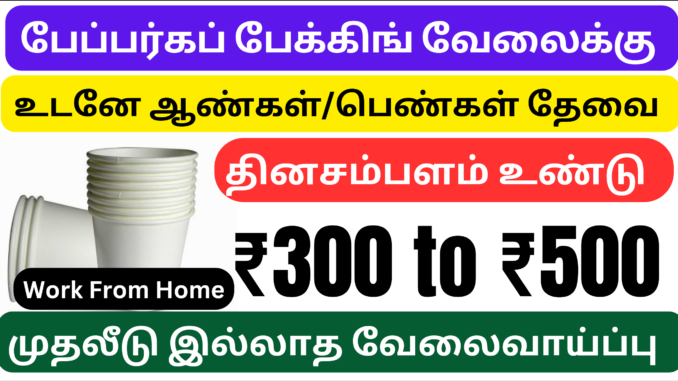
Packing jobs from home tamil / Packing business at home / Best packing job / Work from home
Paper cup making process into 1000 words
Crafting paper cups is a meticulous process involving several stages, each crucial in ensuring the final product meets quality standards. From raw material selection to packaging, every step plays a vital role in producing these ubiquitous vessels used for beverages worldwide. In this narrative, we’ll delve into the intricate process of making paper cups, detailing each phase in around 1000 words.
Raw Material Selection and Preparation
The journey of a paper cup begins with the careful selection of raw materials. The primary material used in manufacturing paper cups is paperboard, a sturdy yet flexible material derived from wood pulp. The chosen paperboard must meet specific criteria, including thickness, stiffness, and ability to hold liquid without leakage.
Once the appropriate paperboard is selected, it undergoes a series of preparation steps. Initially, the paperboard rolls are unwound and inspected for any defects or impurities. Any flawed sections are trimmed to ensure uniformity in the final product. The paperboard is then coated with a thin layer of polyethylene (PE) to provide a waterproof barrier, essential for containing liquid contents without seepage.
Printing and Design
After the paperboard is prepared, it moves to the printing phase. This stage is crucial as it imparts the visual appeal and branding elements to the paper cups. Advanced printing technologies, such as flexography or offset printing, are employed to achieve high-quality graphics and vibrant colors on the paper surface.
Design considerations are paramount during this process, as the printed artwork serves not only aesthetic purposes but also provides essential information such as product branding, volume capacity, and usage instructions. Once the printing is complete, the paperboard is inspected again to ensure accuracy and adherence to design specifications.
Die Cutting and Forming
With the printing done, the paperboard sheets proceed to the die-cutting and forming stage. Here, specialized machinery cuts the paperboard into precise shapes corresponding to the size and design of the intended cups. The die-cutting process ensures consistency in cup dimensions and facilitates efficient forming in subsequent steps.
Following die-cutting, the formed paperboard blanks are transferred to the cup-forming machines. These machines utilize heat and pressure to mold the paperboard into the distinctive conical shape of a cup. Simultaneously, the bottom of the cup is sealed to prevent leakage. The formed cups are then ejected from the machine onto a conveyor belt, ready for the next phase.
Rim Rolling and Curling
Upon exiting the forming machine, the paper cups undergo rim rolling and curling. This step involves rolling the upper edge of the cup to reinforce its rigidity and provide a smooth, comfortable drinking surface. Automated rim rolling machines precisely shape the rim while ensuring a consistent finish across all cups.
Additionally, some cups may require curling, where the rim is turned inward to create a lip, enhancing structural integrity and preventing splashes during use. The rim rolling and curling process are crucial for both functional and aesthetic reasons, contributing to the overall usability and appearance of the final product.
Quality Control and Inspection
Quality control is paramount throughout the paper cup manufacturing process. At various stages, trained personnel conduct inspections to detect any defects or irregularities that may compromise the cups’ integrity or performance. Advanced sensors and monitoring systems are also employed to ensure consistency and accuracy in cup dimensions, printing quality, and sealing integrity.
Defective cups are promptly identified and removed from the production line to prevent them from reaching the market. This rigorous quality control regimen helps uphold the manufacturer’s reputation for producing high-quality, reliable paper cups that meet stringent industry standards.
Packaging and Distribution
Once the paper cups pass the final inspection, they proceed to the packaging phase. Here, automated machinery stacks the cups into predetermined quantities and encases them in outer packaging, such as cardboard boxes or shrink-wrap film. Packaging may include additional branding elements or product information for retail display purposes.
After packaging, the paper cups are ready for distribution to various destinations, including retail stores, restaurants, cafes, and other establishments. Efficient logistics networks ensure timely delivery to meet customer demand while minimizing transit times and costs.
Environmental Considerations
Throughout the paper cup manufacturing process, environmental sustainability is a key consideration. Manufacturers strive to minimize waste generation, optimize resource usage, and employ eco-friendly materials and practices wherever possible. For example, efforts to reduce paper waste may include recycling scrap paperboard and utilizing renewable energy sources to power manufacturing operations.
Furthermore, many manufacturers offer paper cups that are certified compostable or made from recycled materials, catering to consumers’ growing demand for environmentally responsible products. By prioritizing sustainability initiatives, manufacturers aim to minimize the environmental impact of their operations and contribute to a more sustainable future.
In conclusion, the journey of a paper cup from raw material to finished product is a complex yet meticulously orchestrated process. Each stage, from raw material selection to packaging, requires precision, attention to detail, and adherence to quality standards to ensure the final product meets customer expectations. By leveraging advanced technologies, stringent quality control measures, and a commitment to environmental sustainability, paper cup manufacturers continue to deliver innovative solutions for beverage containment while minimizing their environmental footprint.
How to packing paper cup :
Packing paper cups efficiently is essential for ensuring they reach their destination intact and ready for use. Whether you’re packaging paper cups for shipping, storage, or distribution, following proper packing techniques is crucial. Here’s a comprehensive guide on how to pack paper cups effectively:
Gather Necessary Supplies:
Before you begin packing, ensure you have all the required materials:
Sturdy cardboard boxes or cartons
Packing tape
Bubble wrap or packing paper
Packing peanuts or air pillows (optional)
Labels and markers for identification
Prepare the Packing Area:
Choose a clean and spacious area to pack the paper cups. Clear any clutter and make sure the surface is flat and even to prevent cups from tipping over.
Group Cups by Size and Type:
Sort the paper cups based on their size and type. This will help streamline the packing process and ensure efficient use of space in the packaging boxes.
Wrap Individual Cups:
Wrap each paper cup with bubble wrap or packing paper to provide cushioning and protection against damage during transit. Secure the wrapping with tape to keep it in place.
Layering in Boxes:
Start by placing a layer of packing peanuts or air pillows at the bottom of the cardboard box to create a cushioning base. Then, arrange the wrapped paper cups in a single layer, ensuring they are snugly packed but not overly tight to avoid crushing.
Dividers for Stability:
For larger shipments or to prevent cups from shifting during transit, consider using cardboard dividers or inserts between layers. These dividers provide additional stability and protect the cups from rubbing against each other.
Fill Empty Spaces:
Fill any remaining gaps in the box with packing peanuts, air pillows, or additional packing paper to prevent movement and ensure the cups stay in place throughout transportation.
Seal Boxes Securely:
Once the box is filled, securely seal it with packing tape. Reinforce the seams and edges of the box to prevent it from bursting open during handling.
Label Boxes:
Clearly label each box with information such as contents, quantity, and any special handling instructions. This will help both you and the recipient identify the contents easily.
Store or Ship Boxes Properly:
Store the packed boxes in a dry, cool area away from direct sunlight and moisture. If shipping the boxes, choose a reputable carrier and ensure they handle the packages with care to minimize the risk of damage.
Quality Check:
Before shipping or storing the packed boxes, perform a final quality check to ensure everything is properly secured and labeled.
Documentation:
Keep a record of the packed boxes, including their contents and destination, for reference purposes.
By following these steps, you can efficiently pack paper cups to ensure they remain safe and intact during transportation or storage. Effective packing not only protects the cups but also reflects positively on your business’s professionalism and commitment to quality.
Advantage & disadvantages paper cup packing job?
Working in paper cup packing jobs, like any other occupation, has its own set of advantages and disadvantages. Let’s explore both:
Advantages:
Steady Employment: Paper cup packing jobs often provide steady employment opportunities, especially in areas where there is a demand for disposable products like paper cups.
Minimal Skills Required: Generally, these jobs don’t require extensive education or specialized skills. Most tasks can be easily learned on the job, making it accessible to a wide range of people.
Teamwork: Packing jobs often involve working as part of a team, fostering a sense of camaraderie and collaboration among coworkers.
Structured Environment: These jobs usually have clearly defined tasks and routines, providing a structured work environment that some individuals may find comforting and predictable.
Entry-Level Position: Paper cup packing jobs can serve as entry-level positions in the manufacturing industry, offering opportunities for career growth and advancement within the company.
Disadvantages:
Repetitive Tasks: Packing jobs can involve monotonous and repetitive tasks, which may lead to boredom and decreased job satisfaction over time.
Physical Demands: Some packing jobs require standing for long periods or repetitive motions, which can lead to physical strain and fatigue.
Low Wages: In some cases, paper cup packing jobs may offer lower wages compared to other occupations with similar skill requirements.
Limited Advancement Opportunities: While entry-level positions may be readily available, advancement opportunities within the packing department or the company as a whole may be limited without further education or specialized training.
Job Insecurity: Depending on the market demand for paper cups and the stability of the company, there may be fluctuations in job security, with potential for layoffs or reduced hours during slow periods.
Overall, whether a paper cup packing job is advantageous or disadvantageous depends on individual preferences, career goals, and the specific circumstances of the job and employer.
Leave a Reply