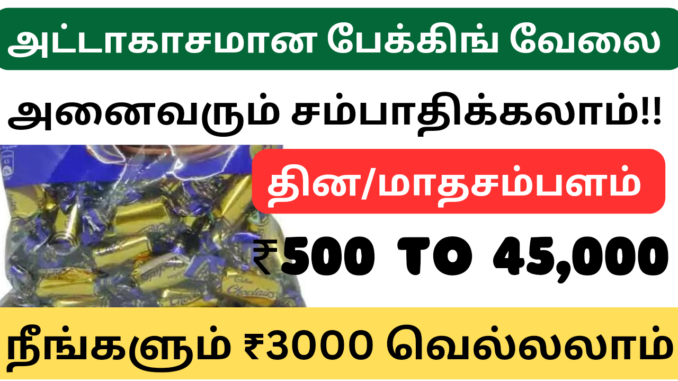
Packing jobs from home / Packing jobs at home / Packing business at home / Home based packing jobs
Paper plate manufacturing :
Paper Plate Manufacturing: A Comprehensive Overview
Paper plates have become a ubiquitous item in modern dining, thanks to their convenience, affordability, and environmental benefits. The manufacturing process behind these seemingly simple products involves a series of intricate steps designed to ensure quality, functionality, and cost-effectiveness. This overview will delve into the various stages of paper plate manufacturing, from raw material selection to the final product.
Raw Material Selection
The primary raw material for paper plates is paper, typically derived from wood pulp. The pulp is obtained through a process called pulping, where wood chips are broken down into fibers. These fibers are then cleaned and refined to produce paper. The quality of the paper used in manufacturing paper plates is crucial, as it affects the plate’s strength and durability.
There are two main types of pulp used: mechanical and chemical. Mechanical pulp is produced by grinding wood, which retains most of the fiber, but results in a lower quality paper. Chemical pulp, on the other hand, is produced using chemicals to dissolve lignin (the substance that binds fibers together), resulting in higher-quality paper with better strength and whiteness.
Paper Preparation
Once the pulp is prepared, it is mixed with water and other additives to form a slurry. This slurry is then fed into a paper machine, where it is spread onto a moving screen to remove excess water. The paper is then pressed and dried to form sheets. For paper plates, the sheets are often coated with a layer of plastic or wax to make them resistant to liquids and grease.
Plate Formation
The dried paper sheets are cut into circles or other desired shapes, depending on the plate design. The cut pieces are then pressed into plate shapes using molds. There are two main methods for this:
Single-Use Plates: These are typically formed from a single sheet of paper that is pressed into shape. The process involves using a press with a mold that shapes the paper into the plate’s form. This method is generally used for standard, disposable paper plates.
Layered Plates: For more robust plates, multiple layers of paper are used. These layers are glued together and then pressed into shape. This method increases the plate’s strength and can make it more resistant to bending and breaking.
Coating and Finishing
To enhance the paper plates’ durability and functionality, they are coated with a protective layer. Common coatings include:
Plastic Coating: This coating makes the plates water-resistant and greaseproof. It is often made from polyethylene or other plastic materials. The coating is applied either by dipping the plates into a plastic solution or by applying it through a spraying process.
Wax Coating: Wax coating provides a similar level of water resistance and is often used for plates that are intended to be biodegradable. The wax is applied in a molten form and then allowed to cool and solidify.
After coating, the plates undergo a quality check to ensure there are no defects in the coating or the paper itself. Plates are also often stamped or printed with designs, logos, or other customizations during this phase.
Quality Control
Quality control is an essential part of the manufacturing process. It involves several checks to ensure that the plates meet industry standards and customer expectations. Some common quality control measures include:
Strength Testing: Plates are tested for strength and durability to ensure they can hold up under normal use.
Water Resistance Testing: The effectiveness of the coating is checked by exposing the plates to water and oil to ensure they do not become soggy or weak.
Visual Inspection: Plates are inspected for any visual defects, such as uneven coating, cracks, or deformities.
Packaging and Distribution
Once the paper plates pass quality control, they are packaged for distribution. Packaging is designed to protect the plates during transport and to make them easy to handle. Plates are typically stacked and wrapped in plastic or cardboard to keep them clean and organized.
The packaged plates are then distributed to retailers, wholesalers, or directly to customers. The distribution process involves logistics and supply chain management to ensure timely and efficient delivery.
Environmental Considerations
With increasing environmental awareness, the paper plate manufacturing industry has made strides in reducing its environmental impact. Several initiatives include:
Recycling: Many manufacturers use recycled paper in their production processes, which helps reduce the demand for virgin wood pulp and minimizes waste.
Biodegradable Coatings: Manufacturers are increasingly using biodegradable coatings and materials to make the plates more environmentally friendly.
Sustainable Sourcing: Efforts are being made to source raw materials from sustainable forests and to use environmentally responsible practices throughout the manufacturing process.
Future Trends
The future of paper plate manufacturing is likely to be influenced by several trends, including:
Increased Demand for Eco-Friendly Products: As consumers become more environmentally conscious, there will be a growing demand for paper plates that are fully biodegradable and made from sustainable materials.
Technological Advancements: Innovations in manufacturing technology may lead to more efficient production processes, better quality control, and improved environmental performance.
Customization and Design: Advances in printing and coating technologies will allow for more customization and design options, catering to diverse consumer preferences and market needs.
The manufacturing of paper plates is a complex process that combines raw material preparation, paper formation, coating, quality control, and distribution. The industry has made significant advancements in terms of environmental sustainability and product quality. As consumer preferences and environmental concerns evolve, the paper plate manufacturing industry will continue to adapt and innovate, ensuring that these everyday items remain practical, affordable, and eco-friendly.
How to Packing paper plates :
Packing paper plates efficiently involves a combination of organization, careful handling, and appropriate materials to ensure they arrive at their destination in pristine condition. Here’s a comprehensive guide on how to pack paper plates, explained in detail to cover approximately 1000 words.
1. Gather Your Supplies
Before you begin packing, make sure you have all the necessary materials. Here’s a list of what you’ll need:
Sturdy Boxes: Choose boxes that are strong enough to support the weight of the plates and are slightly larger than the number of plates you plan to pack. Double-walled corrugated boxes are ideal.
Packing Paper: Use clean, white packing paper to cushion and protect the plates. Avoid newspaper as it might transfer ink onto the plates.
Bubble Wrap: This adds an extra layer of protection, especially if the plates are fragile or high-quality.
Packing Tape: Ensure you have a roll of strong packing tape to seal the boxes securely.
Markers: For labeling the boxes to identify their contents and handling instructions.
2. Prepare the Paper Plates
Before you start packing, inspect the paper plates for any damage or defects. If you find any, set them aside as they might compromise the integrity of the other plates. Ensure all plates are dry and clean to avoid any potential damage during transport.
3. Separate the Plates
Depending on the number of plates and their size, you might need to pack them in smaller, manageable stacks. Separate the plates into stacks of 20 to 25 plates. This makes it easier to handle and reduces the risk of the plates getting damaged due to excessive weight.
4. Wrap the Plates
Each stack of plates should be wrapped individually to provide cushioning and prevent them from rubbing against each other. Here’s how to do it:
Layer Packing Paper: Lay a sheet of packing paper flat on a surface. Place a stack of plates on top of it.
Wrap Each Stack: Gently fold the packing paper around the stack of plates, making sure to cover all sides. For extra protection, use multiple layers of paper if needed.
Secure with Tape: Once wrapped, secure the packing paper with tape to keep it in place.
5. Use Bubble Wrap (Optional)
For added protection, especially for high-quality or delicate plates, you can use bubble wrap:
Wrap the Stacks: After wrapping the plates in packing paper, place the wrapped stacks on a sheet of bubble wrap. Roll the bubble wrap around the stack and secure with tape.
6. Prepare the Boxes
Line the bottom of your boxes with a layer of packing paper or bubble wrap. This creates a cushioning layer that helps protect the plates from any bumps or jolts during transit.
7. Pack the Plates into the Boxes
Carefully place the wrapped stacks of plates into the prepared boxes. Make sure to pack them tightly but without forcing them in, as this could cause damage:
Arrange Stacks: Place the stacks vertically in the box, similar to how books are placed in a box. This orientation provides better support and prevents the plates from shifting.
Add Cushioning: Fill any empty spaces in the box with additional packing paper or bubble wrap to prevent movement. This extra cushioning helps absorb shocks and prevents the plates from moving around.
8. Seal and Label the Boxes
Once all the plates are packed into the boxes, seal them securely with packing tape. Make sure the tape is applied firmly along all seams and edges.
Label Clearly: Use markers to label the boxes with “Fragile” or “Handle with Care” to alert handlers about the contents. Additionally, you can label the boxes with the number of plates inside and any other relevant information, such as the destination or the room where they should be placed.
9. Check and Double-Check
Before you move the boxes, double-check to ensure they are securely sealed and properly labeled. Verify that the packing is tight and that there is no risk of the plates shifting during transport.
10. Transport with Care
When moving the packed boxes, handle them gently. Avoid dropping or tossing the boxes, as this could cause damage to the plates inside. If possible, place the boxes in a secure location where they won’t be jostled around too much during transport.
11. Unpacking
When you arrive at your destination, carefully unpack the boxes. Remove the packing paper and bubble wrap, and inspect each plate for any damage. If any plates are broken or damaged, make a note of it for potential claims if they were insured during transport.
Conclusion
Packing paper plates properly requires careful attention to detail and the right materials. By following these steps, you can ensure that your plates are well-protected and arrive at their destination in excellent condition. Proper packing not only protects your items but also makes the unpacking process smoother and more organized.
Leave a Reply