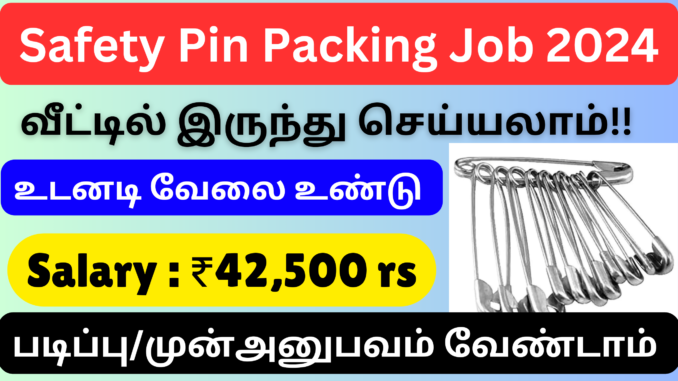
Packing jobs from home / Best packing jobs tamil / Packing business at home / Part time jobs for
Safety pin packing process :
The safety pin packing process is a meticulous and carefully designed system that ensures the pins are securely and efficiently packaged for distribution. This process involves several key stages, from manufacturing to final packaging, each incorporating quality control measures to maintain the safety and reliability of the pins. Here’s a comprehensive overview of the safety pin packing process:
1. Manufacturing and Initial Quality Control
Before the packing process begins, safety pins are manufactured using high-quality metal wire, typically steel or brass. The wire is cut, bent, and shaped into the familiar pin configuration using automated machinery.
Wire Cutting and Shaping: Metal wire is fed into a cutting machine where it is segmented into specific lengths.
Forming the Pin: The cut wire segments are then transferred to forming machines, which bend and twist the wire into the pin shape, including the coiled spring and the clasp.
Quality control at this stage involves inspecting the wire for consistent thickness and strength, ensuring the pins are uniformly shaped, and checking for any defects such as sharp edges or weak points.
2. Surface Treatment
Post-manufacturing, the pins undergo surface treatment to enhance their durability and appearance. This often includes:
Polishing: To remove any rough edges and give the pins a smooth finish.
Plating: A layer of nickel, zinc, or another metal is applied to prevent rust and corrosion. This process can be electroplating or mechanical plating.
Again, quality control measures are applied to ensure that the plating is uniform and adheres well to the metal surface, preventing future peeling or rusting.
3. Sorting and Counting
After surface treatment, the pins are sorted and counted. This step is crucial to ensure each package contains the correct number of pins. Automated sorting machines are typically used:
Sorting Machines: These machines separate the pins, orienting them in a uniform direction for easier counting and packaging.
Counting Machines: Advanced counting mechanisms ensure each batch contains the exact number of pins required for packaging.
Quality control checks involve verifying the accuracy of the sorting and counting machines regularly to prevent discrepancies.
4. Packaging Preparation
The next step is preparing the packaging materials. Depending on the brand and customer requirements, safety pins can be packed in various types of packaging such as plastic boxes, blister packs, or paper envelopes.
Design and Printing: Packaging materials are designed and printed with brand logos, safety instructions, and other necessary information. This step ensures compliance with regulatory standards and brand guidelines.
Pre-folding and Assembly: Packaging materials are pre-folded and assembled as needed to streamline the packing process.
5. Manual or Automated Packing
The sorted and counted pins are now ready to be packed. Depending on the scale of production and the type of packaging, this step can be manual, automated, or a combination of both.
Manual Packing: Workers place the correct number of pins into each package. Manual packing is often used for smaller batches or specialty products.
Automated Packing: Automated machines fill each package with the predetermined number of pins. These machines can handle large volumes and ensure consistency in packing.
During this stage, quality control inspectors check the filled packages to ensure they contain the correct number of pins and that the pins are properly enclosed.
6. Sealing and Final Quality Control
Once the pins are packed, the packages need to be sealed. This can be done through various methods depending on the packaging type:
Heat Sealing: Common for plastic packaging, where the edges of the packaging are sealed using heat.
Adhesive Sealing: Used for paper envelopes and some types of blister packs, where adhesive strips are applied to seal the package.
Final quality control checks are crucial here. Inspectors verify that each package is properly sealed, ensuring there are no openings through which pins could escape. They also check for any packaging defects such as misprints, incorrect labeling, or damaged materials.
7. Batch Coding and Tracking
For inventory and quality control purposes, each batch of packaged safety pins is coded and tracked. This step involves:
Batch Coding: Assigning a unique code to each batch that indicates the date of production, batch number, and other relevant information.
Tracking: Using software systems to track the movement of each batch from the production facility to distribution centers and eventually to retailers or customers.
This tracking system helps in recalling products if any defects are found later and provides transparency in the supply chain.
8. Storage and Distribution
The final stage involves storing the packed safety pins and preparing them for distribution. This includes:
Storage: Keeping the packed safety pins in a controlled environment to prevent any damage or deterioration. Storage conditions such as temperature and humidity are monitored.
Distribution: Organizing the packed pins for shipment. This involves palletizing, labeling, and loading the products onto transportation vehicles.
9. Compliance and Safety Measures
Throughout the entire process, compliance with safety standards and regulations is maintained. This involves:
Regulatory Compliance: Ensuring the entire process meets industry standards and regulations, such as those set by consumer safety organizations.
Employee Safety: Implementing safety measures for workers, including protective gear and training on safe handling of materials and machinery.
The safety pin packing process is a multi-faceted system designed to ensure that each pin is safely and securely packaged. From manufacturing to distribution, each stage involves rigorous quality control measures to maintain the integrity and reliability of the safety pins. The integration of automated systems, meticulous manual inspections, and stringent compliance standards ensures that consumers receive high-quality, safe, and dependable safety pins.
How to make safety pin packing :
Sure! Here is a comprehensive 1000-word guide on the process of packing safety pins, covering the materials required, steps involved, and best practices to ensure safety and efficiency.
Introduction
Safety pins are small, versatile tools used for various purposes, from securing fabric to emergency repairs. Proper packing of safety pins is crucial to ensure they reach consumers safely and in good condition. This guide details the materials, steps, and best practices for packing safety pins, ensuring both efficiency and safety.
Materials Required
Safety Pins: The primary item to be packed.
Packaging Boxes: Sturdy cardboard boxes for bulk packaging.
Inner Packaging: Smaller containers, such as plastic boxes or envelopes, to hold a specific number of safety pins.
Packaging Materials: Bubble wrap, foam, or tissue paper to provide cushioning.
Labeling Supplies: Labels, markers, and printers for product information.
Sealing Materials: Tape, glue, or other sealing methods to secure the packaging.
Safety Gear: Gloves and protective clothing for handling the safety pins.
Step-by-Step Process
1. Preparation
Workspace Setup:
Ensure a clean, organized workspace.
Keep all materials within easy reach.
Safety Measures:
Wear gloves to prevent injury from sharp points.
Use protective clothing if necessary.
2. Sorting
Quality Check:
Inspect safety pins for defects or damage.
Discard any that do not meet quality standards.
Sorting by Size:
If packing multiple sizes, sort safety pins accordingly.
3. Inner Packaging
Choosing Inner Packaging:
Select appropriate inner packaging based on the quantity and size of safety pins.
Counting and Arranging:
Count the safety pins accurately.
Arrange them neatly within the inner packaging.
Securing Inner Packaging:
Use tape or other sealing methods to secure the inner packaging.
Ensure the safety pins are not loose to avoid damage during transit.
4. Labeling
Creating Labels:
Include essential information such as size, quantity, brand, and safety warnings.
Use clear, legible fonts and durable labels.
Applying Labels:
Attach labels to the inner packaging securely.
Ensure labels are visible and not obstructed.
5. Outer Packaging
Choosing Outer Packaging:
Select sturdy cardboard boxes that can withstand shipping conditions.
Adding Cushioning:
Place bubble wrap, foam, or tissue paper at the bottom of the box.
Placing Inner Packaging:
Arrange the inner packages within the outer box.
Ensure they fit snugly to prevent movement.
Adding Additional Cushioning:
Fill any gaps with cushioning materials to protect the safety pins.
Sealing the Box:
Use strong tape to seal the outer box securely.
Reinforce corners and edges for extra protection.
6. Final Labeling
Outer Box Labels:
Attach labels to the outer box with shipping information, handling instructions, and product details.
Use weather-resistant labels if shipping internationally.
Standard Operating Procedures (SOPs):
Establish SOPs for packing to ensure consistency and quality.
Training Employees:
Train employees on proper packing techniques and safety measures.
Efficiency
Automation:
Use automated counters and packagers for large-scale operations to increase efficiency.
Organization:
Keep the workspace organized and maintain an inventory of materials to avoid delays.
Safety Considerations
Handling Safety Pins
Avoiding Injury:
Handle safety pins with care to avoid pricks and cuts.
Use tools such as tweezers for better precision.
Packaging Safety
Material Safety:
Ensure all packaging materials are non-toxic and safe for use.
Avoid using materials that could react with the metal of the safety pins.
Environmental Considerations
Eco-Friendly Materials:
Use recyclable or biodegradable packaging materials whenever possible.
Waste Reduction:
Minimize waste by optimizing the size of the inner and outer packaging.
Conclusion
Packing safety pins may seem straightforward, but it requires careful attention to detail to ensure the safety and satisfaction of consumers. By following the outlined steps and best practices, you can efficiently pack safety pins while maintaining high standards of quality and safety. Whether you are packing for retail, wholesale, or personal use, these guidelines will help you achieve a professional and secure packaging solution.
References
Industry Standards for Packaging: Consult relevant industry standards for packaging to ensure compliance.
Safety Guidelines: Refer to safety guidelines for handling sharp objects.
Environmental Regulations: Stay updated with environmental regulations regarding packaging materials.
This comprehensive guide covers all aspects of packing safety pins, ensuring both efficiency and safety in the process.
Leave a Reply