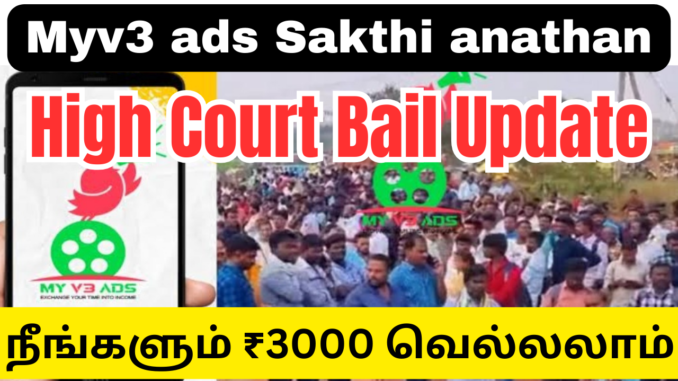
Packing jobs at home / Work from home / Packing jobs from home / Earn money online tamil
Peanut candy packing work :
Sure, here’s an overview of the process of packing peanut candy, breaking it down into around 1000 words:
Peanut Candy Packing Process: A Comprehensive Overview
The packing of peanut candy involves several stages, each crucial to ensure the product is presented well and remains fresh for consumers. This process combines both automated and manual techniques, depending on the scale of production and the specific requirements of the candy. Here’s a detailed look at the key steps involved.
1. Preparation and Quality Control
a. Ingredient Quality Check: Before packing begins, it’s essential to ensure that the peanut candy ingredients meet quality standards. This involves inspecting peanuts for freshness, checking sugar levels, and ensuring any additional flavorings or coatings are of high quality. Quality control teams test samples for taste, texture, and adherence to safety standards.
b. Production Check: Once ingredients are approved, the production line is set up and calibrated. This includes ensuring that machines for mixing, cooking, and forming the candy are in optimal working condition. Regular maintenance and calibration are critical to prevent inconsistencies in the final product.
2. Production Process
a. Cooking and Mixing: The peanut candy production starts with the cooking and mixing of ingredients. Peanuts are roasted or otherwise prepared according to the recipe. Sugar, syrups, and any other flavorings are combined and cooked to the desired consistency. This mixture is then combined with the peanuts, often in a large mixing vessel.
b. Forming and Shaping: The candy mixture is then transferred to forming machines. Depending on the type of peanut candy being produced (e.g., peanut brittle, peanut clusters), this step involves shaping the candy into the desired form. This could be through extrusion, molding, or cutting. Precision is key to ensure uniform size and appearance.
c. Cooling: Once shaped, the candies need to cool down to solidify properly. This step is crucial for maintaining the texture and structure of the candy. Cooling tunnels or air-cooled conveyors are often used, allowing the candy to cool at a controlled rate.
3. Inspection and Quality Control
a. Visual Inspection: Before packing, each piece of candy undergoes a visual inspection. This step helps to identify any defects such as uneven shapes, cracks, or imperfections. Automated cameras and manual checks are employed to ensure that only candies meeting the quality standards proceed to the next stage.
b. Weight Check: Candy pieces are weighed to ensure they meet the specified weight requirements. This is important for maintaining consistency and compliance with packaging regulations. Automated scales are often used to check and sort candies based on weight.
4. Packaging Materials
a. Selection: Choosing the right packaging material is crucial for protecting the candy and extending its shelf life. Materials commonly used include plastic wraps, foil pouches, and paper boxes. The choice depends on factors such as product type, shelf life, and marketing requirements.
b. Design and Printing: Packaging design involves not only the visual aspects, such as branding and product information, but also functional elements like seals and closures. Labels and packaging are often printed with nutritional information, ingredient lists, and expiry dates.
5. Packing Process
a. Automated Packing: In high-volume production settings, automated packing machines handle the bulk of the packing process. These machines fill containers or wrappers with a specified amount of candy, seal them, and prepare them for shipping. Automated systems ensure high efficiency and consistency.
b. Manual Packing: For smaller production runs or specialty items, manual packing may be employed. Workers carefully place candies into packaging, ensuring each piece is placed neatly and that packaging is sealed correctly. This method allows for more flexibility and attention to detail but is slower than automated packing.
c. Sealing and Labeling: Once packed, the candy is sealed to protect it from environmental factors such as moisture and air. Labels are applied, including batch numbers and expiration dates. This information is crucial for traceability and consumer information.
6. Final Quality Checks
a. Sealing Integrity: After packaging, it’s important to check the integrity of the seals to ensure that the candy is protected from contamination. This might involve inspecting the packaging for any defects or leaks.
b. Random Sampling: A sample of finished products is often taken for a final quality check. This can include tasting, checking for correct labeling, and ensuring that packaging meets the specified standards.
7. Storage and Distribution
a. Storage Conditions: Proper storage conditions are essential to maintain the quality of the candy. The storage area should be cool, dry, and free from pests. Proper shelving and handling practices prevent damage to the packaging and ensure that the candy remains in optimal condition.
b. Distribution: Once packed, the candy is ready for distribution. Logistics teams ensure that products are transported to retailers or distribution centers in a timely manner. This involves careful handling and transportation to prevent damage.
8. Regulatory Compliance
a. Food Safety Regulations: Compliance with food safety regulations is mandatory. This includes adhering to standards set by organizations such as the Food and Drug Administration (FDA) or other local regulatory bodies. Regular audits and inspections ensure that all practices meet legal and safety requirements.
b. Environmental Considerations: Sustainable practices in packaging and waste management are increasingly important. Many companies are exploring eco-friendly packaging options and implementing recycling programs to reduce their environmental impact.
Packing peanut candy is a detailed process that involves careful planning and execution to ensure the final product is safe, attractive, and of high quality. From initial ingredient checks to final quality inspections, each step is crucial to delivering a product that meets consumer expectations and regulatory standards. By combining advanced technology with meticulous manual processes, manufacturers can achieve efficient production and high-quality outcomes in the competitive candy market.
How to work packing jobs :
craft a comprehensive 1000-word guide on working in packing jobs, you’ll want to cover various aspects including job responsibilities, skills required, work environment, and tips for success. Here’s a structured approach to ensure you include all essential information:
Working in Packing Jobs: A Comprehensive Guide
Introduction
Packing jobs are crucial in many industries, including manufacturing, logistics, and retail. These roles involve preparing products for shipment, ensuring that they are secure and ready for delivery. This guide covers the key responsibilities, skills needed, work environment, and tips for success in packing jobs.
1. Responsibilities in Packing Jobs
Packing jobs encompass a range of responsibilities, including:
Product Inspection: Before packing, workers must inspect items for quality and damage. This ensures that only products that meet quality standards are shipped to customers.
Packing Items: Workers must carefully pack products into boxes or containers. This involves selecting the appropriate packing materials, such as bubble wrap or foam peanuts, to protect items during transit.
Labeling: Accurate labeling is crucial for ensuring that shipments are correctly identified and routed. Workers often need to affix labels with shipping information, barcodes, and other relevant details.
Inventory Management: Packing jobs often involve maintaining accurate inventory records. Workers need to track the quantities of products being packed and report any discrepancies.
Adhering to Safety Standards: Ensuring that packing procedures adhere to safety regulations is essential. This includes following proper lifting techniques and using personal protective equipment (PPE) when necessary.
2. Essential Skills for Packing Jobs
To excel in packing jobs, certain skills and qualities are beneficial:
Attention to Detail: Precision is crucial in packing to ensure that products are packed correctly and labels are accurate. Mistakes can lead to shipping errors and customer dissatisfaction.
Physical Stamina: Packing can be physically demanding, requiring standing for long periods, lifting heavy boxes, and performing repetitive tasks. Good physical stamina and strength are important.
Organizational Skills: Effective organization helps in managing packing tasks efficiently. Being able to prioritize tasks and maintain a clean work area contributes to a smoother workflow.
Problem-Solving Skills: Sometimes, unexpected issues arise, such as damaged products or incorrect packing materials. The ability to quickly find solutions is important.
Teamwork and Communication: Packing jobs often involve working as part of a team. Good communication and the ability to collaborate effectively with colleagues are important for a harmonious work environment.
3. Work Environment in Packing Jobs
Packing jobs can be found in various settings, including:
Warehouses: Many packing jobs are situated in large warehouses where products are stored and prepared for shipment. Warehouses can be fast-paced environments with a focus on efficiency.
Manufacturing Facilities: In manufacturing settings, packing jobs may involve packing products directly from the production line. This environment may be noisy and require adherence to strict safety protocols.
Retail Stores: Some retail stores have packing departments where online orders are prepared for shipping. This environment may be more customer-focused and involve a mix of packing and customer service tasks.
Distribution Centers: These centers handle the distribution of products from manufacturers to retailers or customers. Packing jobs here may involve sorting items and preparing large volumes of shipments.
4. Tips for Success in Packing Jobs
To succeed in packing jobs, consider the following tips:
Master the Packing Techniques: Familiarize yourself with various packing methods and materials. Understanding how to pack different types of products effectively can improve efficiency and reduce errors.
Stay Organized: Keep your workspace tidy and organized. An orderly environment helps in maintaining productivity and prevents accidents.
Follow Safety Protocols: Always adhere to safety guidelines to prevent injuries. Use PPE, follow proper lifting techniques, and report any hazards or unsafe conditions immediately.
Be Efficient but Accurate: Strive for a balance between speed and accuracy. While efficiency is important, it should not come at the expense of packing quality.
Seek Feedback: Regularly ask for feedback from supervisors and colleagues. Constructive criticism can help you improve your packing skills and work performance.
Continual Learning: Stay updated with new packing techniques and technologies. Ongoing learning can enhance your skills and open up opportunities for career advancement.
Conclusion
Packing jobs play a vital role in the supply chain, ensuring that products reach customers in excellent condition. By understanding the key responsibilities, developing essential skills, and working effectively in various environments, you can excel in this field. Adhering to best practices and continuously improving your skills will contribute to your success and satisfaction in packing jobs.
Leave a Reply