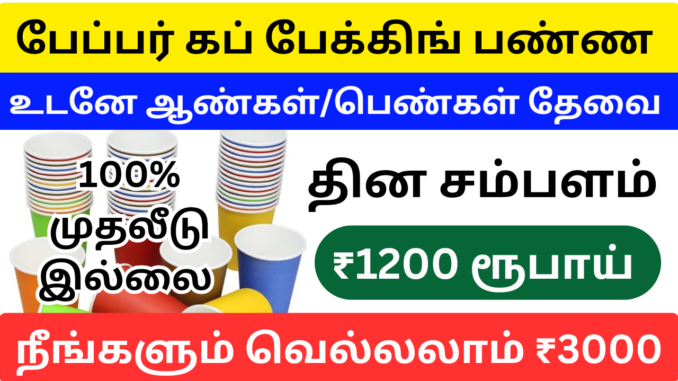
Packing business at home / Packing jobs tamil / Best packing jobs tamil / Work from home
How to packing paper cup industry :
Overview of the Paper Cup Industry
The paper cup industry is a significant segment of the global packaging market, driven by the increasing demand for convenience, sustainability, and hygiene. Paper cups are widely used in various sectors, including food and beverage, healthcare, and retail, owing to their disposability and eco-friendliness compared to plastic alternatives.
Market Trends
Sustainability Focus: With growing environmental concerns, there is an increasing shift toward sustainable products. Many companies are now using recyclable, compostable, and biodegradable materials to produce paper cups.
Technological Advancements: Innovations in coating materials and manufacturing processes have improved the quality and functionality of paper cups, making them suitable for both hot and cold beverages.
Health and Hygiene: The COVID-19 pandemic has heightened awareness around hygiene, leading to a surge in demand for disposable cups in cafes, restaurants, and food service operations.
Customization: Brands are investing in customized paper cups for marketing purposes, using them as a canvas for logos and designs that enhance brand visibility.
Manufacturing Process
The production of paper cups involves several key steps:
Material Sourcing: High-quality paperboard is sourced, typically from sustainable forests. The choice of paperboard is crucial for the cup’s durability and insulation properties.
Coating: A polyethylene or PLA (polylactic acid) coating is applied to make the cups water-resistant. This step is essential for maintaining the integrity of the cup when filled with liquids.
Die-Cutting: The coated paper is then die-cut into cup shapes. This process is automated to ensure precision and efficiency.
Forming: The die-cut pieces are formed into cups using a specialized machine that rolls, folds, and seals the edges.
Quality Control: Cups undergo rigorous testing to ensure they meet safety and performance standards.
Printing: Custom designs or branding elements are printed on the cups, using eco-friendly inks where possible.
Packaging and Distribution: The final products are packaged and shipped to distributors or directly to customers.
Environmental Considerations
While paper cups are often perceived as more environmentally friendly than plastic cups, there are important factors to consider:
Recycling Challenges: The polyethylene lining makes recycling paper cups challenging. Many facilities do not accept them, leading to increased waste in landfills.
Sourcing Practices: Sustainable sourcing of raw materials is critical. Companies are encouraged to obtain certifications (like FSC) to ensure responsible forestry practices.
Biodegradability: Biodegradable options are emerging, utilizing materials that break down more efficiently in composting environments.
Key Players in the Industry
The paper cup industry comprises several key players, including:
Manufacturers: Companies like Dart Container Corporation, Huhtamaki, and International Paper dominate the market, focusing on innovation and sustainability.
Suppliers: Suppliers of raw materials, such as paperboard and coatings, play a crucial role in the supply chain.
Distributors: Wholesalers and distributors facilitate the supply of paper cups to end-users, including restaurants, coffee shops, and food service providers.
Market Challenges
Cost Competitiveness: Paper cups can be more expensive to produce than plastic cups, impacting pricing strategies and market share.
Regulatory Changes: Increasing regulations regarding single-use plastics may influence the market dynamics, necessitating rapid adaptation by manufacturers.
Consumer Preferences: As consumers become more aware of environmental issues, their preferences may shift, affecting demand for specific types of products.
Future Outlook
The future of the paper cup industry appears promising, with several trends expected to shape its development:
Innovative Materials: Continued research and development into sustainable materials will enhance product offerings and reduce environmental impacts.
Increased Demand: As urbanization and a fast-paced lifestyle continue to rise, the demand for convenient packaging solutions like paper cups will likely increase.
Circular Economy Initiatives: Companies are expected to adopt circular economy principles, focusing on recycling and reusing materials to minimize waste.
The paper cup industry is at a crossroads, balancing the demands for convenience and sustainability. With the right innovations and strategies, the industry can thrive while contributing positively to environmental goals.
The integration of advanced manufacturing techniques, sustainable sourcing, and a focus on consumer preferences will determine the future trajectory of this essential market segment. As awareness and demand for eco-friendly solutions grow, the paper cup industry is poised to play a vital role in the packaging landscape.
Paper cup packing methods :
Paper Cup Packing Methods
Paper cups are widely used in various industries, particularly in food service and beverage distribution. Efficient packing methods are crucial for maintaining the quality of the cups and ensuring cost-effective logistics. This article will explore the primary methods of packing paper cups, discussing their advantages, disadvantages, and best practices.
1. Types of Paper Cups
Before delving into packing methods, it’s essential to understand the types of paper cups available. Common varieties include:
Single-Wall Cups: Lightweight and typically used for hot or cold beverages, but require sleeves for hot drinks to prevent burns.
Double-Wall Cups: Insulated and sturdier, these cups can handle hot beverages without additional sleeves.
Lined Cups: Often coated with a polyethylene liner for leak resistance, making them suitable for cold drinks.
2. Packing Methods
A. Bulk Packing
Description: Cups are packed loosely into large boxes without any protective materials.
Advantages:
Cost-effective due to minimal material use.
Quick packing process.
Disadvantages:
High risk of damage during transport.
Cups can become dirty or contaminated.
Best Practices:
Use sturdy boxes designed to withstand weight and pressure.
Ensure boxes are filled to minimize movement.
B. Sleeved Packing
Description: Cups are stacked and packed in sleeves made from cardboard or paper.
Advantages:
Reduces the risk of cups sticking together.
Offers additional protection during transit.
Disadvantages:
Requires additional materials, increasing costs.
More time-consuming than bulk packing.
Best Practices:
Use sleeves that fit snugly to prevent cups from shifting.
Ensure the sleeve material is sturdy enough to handle weight.
C. Stacked Packing
Description: Cups are nested inside each other, often using a cardboard separator.
Advantages:
Maximizes space utilization.
Reduces the risk of crushing during storage and transit.
Disadvantages:
Potential for cups to get stuck together, making them difficult to separate.
Requires careful handling to avoid damage.
Best Practices:
Use separators made of lightweight but sturdy materials.
Ensure proper stacking to prevent toppling.
D. Wrap Packing
Description: Cups are individually wrapped in protective materials, such as plastic or paper.
Advantages:
Offers the highest level of protection against damage and contamination.
Ideal for high-end products or specialized cups.
Disadvantages:
More labor-intensive and costly due to additional materials.
Slower packing process.
Best Practices:
Choose wrapping materials that are durable yet lightweight.
Consider automation for large-scale operations to improve efficiency.
3. Factors Influencing Packing Method Selection
When choosing a packing method, several factors must be considered:
A. Volume of Cups
High-volume orders may benefit from bulk or stacked packing to maximize efficiency. Conversely, smaller orders might warrant sleeved or wrap packing for better protection.
B. Transport Method
The mode of transport—whether by truck, ship, or air—affects the choice of packing. More fragile packing methods may be necessary for longer journeys or less stable transport options.
C. Cup Design
The design and materials of the cups themselves can dictate packing methods. For example, double-wall cups may be more robust and could withstand bulk packing better than single-wall cups.
D. Cost Considerations
Budget constraints play a significant role. While bulk packing may be cheaper, the potential for damage could lead to higher costs in the long run due to product loss and returns.
4. Sustainability Considerations
With increasing emphasis on sustainability, eco-friendly packing methods are gaining traction. Here are some approaches:
Recyclable Materials: Use boxes and packing materials that can be recycled or are made from recycled content.
Minimal Packaging: Strive to reduce the amount of packaging material used without compromising protection.
Biodegradable Options: Explore biodegradable wrapping materials for environmentally conscious consumers.
5. Automation in Packing
As demand for efficiency increases, many companies are turning to automated packing solutions. Automated systems can significantly reduce labor costs, improve speed, and enhance packing consistency. Key technologies include:
Robotic Packing Systems: Robots can handle the stacking and packing of cups, reducing human error and injury risks.
Automated Wrapping Machines: These machines can wrap cups quickly and securely, ensuring consistency in packing.
6. Quality Control Measures
Regardless of the packing method used, implementing quality control measures is essential to ensure that the cups reach customers in optimal condition. This includes:
Inspection: Regular checks of packing materials and methods to ensure they meet quality standards.
Testing: Conducting stress tests on packed boxes to assess their durability during transit.
Feedback Loops: Gathering customer feedback on cup conditions upon arrival to refine packing practices.
7. Conclusion
Efficient packing of paper cups is vital for ensuring product quality and customer satisfaction. The choice of packing method depends on various factors, including volume, transport, design, and cost considerations.
Companies are increasingly prioritizing sustainability and automation to enhance their packing processes. By carefully selecting packing methods and implementing best practices, businesses can reduce waste, minimize damage, and improve overall operational efficiency.
Leave a Reply