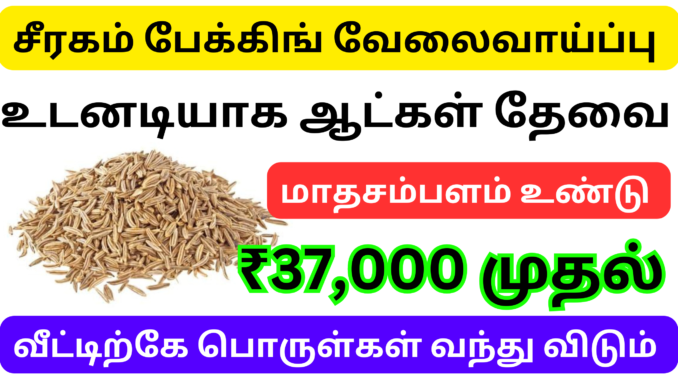
Packing Business at home / Packing jobs at home tamil / work from home job / Earn money online tamil
Cumin Packing Process
Introduction
Cumin (Cuminum cyminum) is a widely used spice in culinary and medicinal applications. Proper packaging ensures the spice retains its aroma, flavor, and quality while extending its shelf life. The cumin packing process involves several key stages, including cleaning, drying, grading, weighing, filling, sealing, labeling, and storage. This document provides an in-depth look at the cumin packing process.
1. Raw Material Procurement
The first step in the cumin packing process is sourcing high-quality cumin seeds from trusted suppliers or farmers. The seeds must meet predefined quality standards in terms of moisture content, purity, color, and aroma.
2. Cleaning and Sorting
Before packaging, cumin seeds undergo thorough cleaning to remove impurities such as dust, dirt, stones, and other foreign materials. The cleaning process includes:
Pre-cleaning: Using sieves and air classifiers to remove large and lightweight impurities.
Magnetic Separation: Removing metallic contaminants using powerful magnets.
Destoning: Separating stones and heavier particles from cumin seeds.
Optical Sorting: Using color sorters to eliminate discolored or defective seeds.
3. Drying Process
Cumin seeds must be dried to an optimal moisture level (typically 8-10%) to prevent mold growth and microbial contamination. The drying process includes:
Sun Drying: Spreading seeds in thin layers under direct sunlight.
Mechanical Drying: Using industrial dryers with controlled temperature settings to ensure uniform drying.
4. Grading
Cumin seeds are graded based on size, color, and purity. Common grading methods include:
Manual Sorting: Handpicking high-quality seeds.
Machine Grading: Using sieves and vibrating graders to classify seeds into different grades based on size and weight.
5. Weighing and Measuring
The graded cumin seeds are weighed accurately to match the predefined packaging sizes. Standard pack sizes include 50g, 100g, 250g, 500g, 1kg, and bulk packs of 25kg or more.
6. Filling Process
The cumin seeds are transferred to packaging machines, where they are filled into different types of packaging materials. The common filling techniques include:
Manual Filling: For small-scale operations.
Automatic Filling: Using volumetric or weight-based filling machines for precise measurements.
7. Sealing and Packaging
Once filled, the packaging must be sealed properly to ensure freshness and prevent contamination. Sealing methods include:
Heat Sealing: For plastic pouches and laminated packaging.
Vacuum Sealing: To remove excess air and enhance shelf life.
Zipper or Resealable Closure: For user convenience.
8. Labeling and Branding
Each packed unit is labeled with important information such as:
Brand Name
Product Name
Net Weight
Batch Number
Manufacturing and Expiry Date
Nutritional Information
Storage Instructions
Barcode for Tracking
9. Quality Control and Inspection
Before the packaged cumin is released for distribution, quality control checks are performed, including:
Moisture Content Analysis: Ensuring proper dryness levels.
Microbial Testing: Checking for bacteria, yeast, and mold growth.
Foreign Material Inspection: Ensuring purity and absence of contaminants.
Weight Accuracy: Confirming the correct amount of product is packed.
Sealing Integrity: Ensuring no leaks or defects in packaging.
10. Storage and Warehousing
After packing, cumin is stored in a dry, cool, and hygienic warehouse to maintain quality. Storage considerations include:
Temperature Control: Keeping storage temperatures between 10-25°C.
Humidity Control: Preventing excess moisture to avoid spoilage.
Pest Control: Using fumigation or safe pest repellents to prevent insect infestation.
11. Distribution and Logistics
Packed cumin is transported to wholesalers, retailers, or directly to consumers. Distribution involves:
Proper Handling: Ensuring minimal damage during transit.
Efficient Supply Chain Management: Using reliable logistics partners.
Cold Chain Logistics (if required): For preserving aroma and quality in extreme climates.
Conclusion
The cumin packing process is a meticulous procedure that ensures high-quality product delivery to consumers. From cleaning and sorting to weighing, filling, sealing, labeling, and storage, every step plays a crucial role in maintaining the integrity of cumin seeds. Following best practices in cumin packaging enhances product safety, market appeal, and shelf life.
How to cumin making method:
Here’s an outline to expand upon:
The Complete Guide to Making Cumin: From Cultivation to Processing
Introduction
Cumin (Cuminum cyminum) is a widely used spice known for its earthy, nutty, and slightly spicy flavor. It is a staple in cuisines worldwide, particularly in Indian, Middle Eastern, and Latin American dishes. This article provides an in-depth guide to cumin production, from farming to the final product.
1. Understanding Cumin
Cumin is a flowering plant from the Apiaceae family, closely related to parsley and coriander. It is cultivated mainly for its seeds, which are dried and used as a spice. Cumin seeds are rich in essential oils that give them their characteristic aroma.
Nutritional and Culinary Importance
High in antioxidants and essential oils
Used in curries, spice blends (garam masala, taco seasoning), soups, and stews
Aids digestion and improves metabolism
2. Cultivation of Cumin
Climate and Soil Requirements
Cumin is a warm-season crop that grows well in arid and semi-arid regions. It requires:
Temperature: 25-30°C (77-86°F)
Soil Type: Well-drained loamy or sandy soil with a pH of 6.8–8.3
Rainfall: Low to moderate rainfall (too much water can cause root rot)
Seed Selection and Sowing
Use high-quality, disease-resistant cumin seeds.
Sow seeds directly into the field, spacing them 20-25 cm apart.
The ideal sowing period is from October to November.
Irrigation and Fertilization
Cumin requires minimal watering. Overwatering can cause fungal infections.
Use organic fertilizers like compost or well-rotted manure to enhance soil fertility.
Pest and Disease Management
Common Pests: Aphids, thrips, and cutworms
Diseases: Fusarium wilt, powdery mildew
Control Methods: Crop rotation, neem oil spray, and organic pesticides
3. Harvesting and Post-Harvest Processing
When to Harvest
Cumin is ready for harvest 100-120 days after sowing when:
The plant turns yellowish-brown.
Seeds harden and develop a strong aroma.
Harvesting Techniques
The plants are uprooted manually or cut using sickles.
Bundles of harvested plants are left in the field for drying.
Drying and Threshing
Dry the harvested cumin in the sun for 5-7 days.
Threshing (separating seeds from plant material) is done using a thresher or by hand.
Cleaning and Grading
Remove impurities using winnowing.
Grade seeds based on size, color, and quality.
4. Processing Cumin for Market
Roasting and Grinding
Cumin seeds can be roasted to enhance flavor.
Ground cumin is made by grinding roasted seeds into a fine powder.
Storage
Store cumin in airtight containers away from light and moisture.
Whole seeds last longer than ground cumin.
5. Conclusion
Cumin production is a detailed process that requires proper climate, care, and post-harvest handling. Whether used as whole seeds or ground powder, cumin remains one of the most valued spices globally.
Benefits of cumin packing?
Packing cumin properly provides several benefits, whether for commercial or personal use. Here are some key advantages:
1. Preservation of Quality
Protects cumin from moisture, air, and light, which can degrade its flavor and aroma.
Prevents contamination from dust, insects, and microbes.
2. Extended Shelf Life
Proper packaging helps retain the essential oils in cumin, keeping it fresh for a longer time.
Reduces spoilage and waste.
3. Convenience in Handling & Storage
Makes transportation easier and more efficient.
Allows for easy stacking and organization in storage.
4. Branding & Marketing
Attractive packaging enhances product appeal and helps in branding.
Provides space for labels with important details like origin, expiry date, and usage instructions.
5. Regulatory Compliance
Meets food safety and quality standards for commercial distribution.
Ensures traceability with batch numbers and barcodes.
6. Cost-Effectiveness
Bulk or vacuum-sealed packaging can reduce transportation and storage costs.
Prevents unnecessary wastage, leading to better profitability.
Leave a Reply