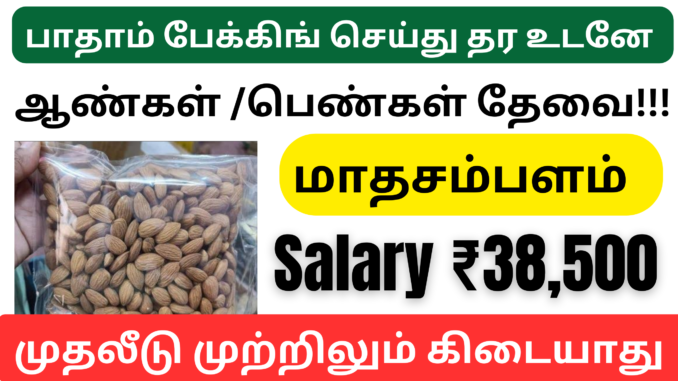
Online jobs / online jobs at home / packing jobs from home / packing jobs tamil 2024
Almond packing process :
The almond packing process is a meticulous operation that ensures the quality and safety of almonds from the farm to the consumer. It involves several critical stages, including sorting, cleaning, drying, inspecting, and packaging. Each step is designed to maintain the integrity of the almonds while meeting industry standards and regulatory requirements. Below is a detailed overview of the almond packing process.
1. Harvesting and Initial Handling
Harvesting:
Almonds are typically harvested from late August to October. The process starts with shaking the almond trees to dislodge the nuts, which fall to the ground and are left to dry for several days.
Sweeping and Pickup:
Once the almonds have dried, mechanical sweepers gather them into rows, and pick-up machines collect the nuts from the orchard floor. The harvested almonds are transported to a hulling and shelling facility.
2. Hulling and Shelling
Hulling:
In the hulling facility, the outer hull of the almond is removed. The almonds are passed through various mechanical devices, including drum hullers and aspiration systems, to separate the hulls from the nuts.
Shelling:
The next step is shelling, where the almond shells are cracked and removed. Shelling machines use rollers or other mechanisms to break the hard shells without damaging the kernels inside. The shelled almonds are then separated from the shell fragments using screening and air classification.
3. Cleaning and Sorting
Pre-Cleaning:
Before further processing, almonds undergo a pre-cleaning stage to remove foreign materials like sticks, stones, and dirt. This is achieved through screening and aspiration systems.
Sizing and Grading:
Almonds are then sized and graded based on their dimensions and quality. Sizing involves passing almonds through sieves with different-sized holes, while grading separates them by color, appearance, and other quality parameters.
Electronic Sorting:
Advanced electronic sorting machines use laser, infrared, and X-ray technologies to detect and remove defective almonds, including those with internal damage, discoloration, or contamination. These machines ensure that only high-quality almonds proceed to the next stage.
4. Blanching (Optional)
Blanching is an optional step, often requested by customers. It involves removing the almond skins by immersing the nuts in hot water and then cooling them rapidly. The blanched almonds are then dried to restore their crunchiness. This process enhances the almonds’ visual appeal and is essential for certain culinary uses.
5. Drying and Moisture Control
After cleaning and sorting, almonds are dried to achieve the desired moisture content, which is typically around 5-6%. Proper drying is crucial to prevent mold growth and ensure the almonds have a long shelf life. Drying can be done using air dryers or other controlled drying systems. Moisture levels are carefully monitored throughout this stage.
6. Final Inspection and Quality Control
Manual Inspection:
Despite advanced technology, manual inspection remains an essential part of the process. Trained personnel visually inspect the almonds on conveyor belts to identify and remove any remaining defective nuts or foreign materials.
Quality Control Testing:
Samples of almonds are taken for laboratory testing to check for aflatoxins, pesticide residues, and other contaminants. This ensures that the almonds meet food safety standards and regulatory requirements.
7. Packaging
Types of Packaging:
Almonds can be packed in various formats, including bulk bags, vacuum-sealed bags, cans, and retail-ready packages. The choice of packaging depends on customer requirements and market preferences.
Packaging Materials:
High-quality, food-grade materials are used for packaging to maintain freshness and protect almonds from moisture, light, and pests. Common materials include plastic, aluminum foil, and laminated films.
Automated Packing:
Modern almond packing facilities use automated systems to fill, weigh, and seal packages. These systems ensure precision and efficiency, reducing human error and contamination risks.
Labeling:
Packages are labeled with essential information, including product name, net weight, nutritional facts, best-before date, batch number, and allergen warnings. Accurate labeling is crucial for traceability and regulatory compliance.
8. Storage and Distribution
Storage Conditions:
Packed almonds are stored in cool, dry conditions to maintain their quality until they are distributed. Temperature and humidity control are vital to prevent spoilage and maintain freshness.
Inventory Management:
Effective inventory management systems track the storage and movement of almond packages. This helps in managing stock levels, fulfilling orders promptly, and ensuring traceability.
Distribution:
Almonds are distributed through various channels, including wholesalers, retailers, and directly to consumers. The logistics process is designed to minimize transit time and protect the almonds from damage during transportation.
9. Sustainability and Waste Management
Sustainability Practices:
The almond industry is increasingly adopting sustainable practices, such as reducing water usage, implementing renewable energy sources, and minimizing waste. Efficient irrigation techniques and solar-powered facilities are examples of such initiatives.
By-Product Utilization:
By-products from the almond packing process, such as shells and hulls, are often repurposed. Almond shells can be used as biofuel or in livestock bedding, while hulls are used as cattle feed, contributing to a zero-waste approach.
The almond packing process is a complex and highly regulated operation that ensures the delivery of safe, high-quality almonds to consumers. From harvesting to distribution, each step is carefully managed to maintain the nuts’ integrity and meet stringent quality standards. Advances in technology, sustainability practices, and rigorous quality control measures all play crucial roles in this process, reflecting the industry’s commitment to excellence and sustainability.
How to make almonds in industry :
Introduction
The almond industry is a complex and multifaceted sector involving various stages from cultivation to the final product. This process includes growing, harvesting, processing, and packaging almonds to meet the high standards expected by consumers worldwide. Almonds are one of the most popular nuts globally, valued for their nutritional benefits, versatility in food products, and economic significance. This essay provides a detailed overview of how almonds are produced in the industry, highlighting each critical stage in the process.
Cultivation of Almonds
Growing Conditions
Almonds thrive in Mediterranean climates, which provide the warm, dry summers and mild, wet winters ideal for their growth. The primary regions for almond cultivation include California in the United States, Spain, and Australia. California, in particular, is the leading producer, accounting for about 80% of the world’s supply.
Planting and Maintenance
Almond trees are typically planted in well-drained soils with good fertility. Proper irrigation is crucial, especially during dry periods, to ensure optimal growth. Almond orchards require a well-designed irrigation system, often using drip irrigation to conserve water and deliver it directly to the roots. Regular maintenance includes pruning to encourage healthy growth and pest control to protect against diseases and insects.
Harvesting Almonds
Timing and Methods
The harvesting period for almonds typically begins in late summer to early fall. The timing is crucial as almonds need to be fully mature before they are collected. Mechanical tree shakers are commonly used to shake the almonds from the trees. The nuts are then left to dry on the ground for several days to reduce moisture content.
Collection and Initial Processing
After drying, almonds are swept into rows and collected using machinery. The collected almonds are then transported to processing facilities where the initial stages of cleaning and hulling begin. Hulling removes the outer green shell, leaving the almond in its hard shell.
Processing Almonds
Shelling and Sorting
In the processing plant, the almonds undergo shelling to remove the hard outer shell. This is done using a series of mechanical crackers and rollers. Once shelled, the almonds are sorted and graded based on size, quality, and appearance. Advanced optical sorters and manual inspection ensure that only the highest quality almonds proceed to the next stages.
Blanching and Roasting
Depending on the end product, almonds may undergo blanching, where they are briefly immersed in hot water to remove the skin. Roasting is another common processing step, enhancing flavor and texture. Roasting can be done either with dry heat or with oil, depending on the desired product.
Packaging and Quality Control
Packaging
Once processed, almonds are packaged for sale. Packaging varies from bulk sacks for industrial use to consumer-ready formats like vacuum-sealed bags, jars, or snack packs. Packaging plays a crucial role in preserving freshness and extending shelf life. Advanced packaging technologies, such as modified atmosphere packaging, are used to maintain the quality of almonds.
Quality Control
Throughout the processing stages, rigorous quality control measures are implemented. These include regular testing for aflatoxins, moisture content, and microbial contamination. Ensuring that almonds meet food safety standards is paramount, and many facilities are certified under global food safety standards like ISO 22000 or the Global Food Safety Initiative (GFSI).
Environmental and Economic Aspects
Environmental Impact
Almond farming has faced scrutiny due to its high water usage, especially in regions like California where water scarcity is a concern. Sustainable farming practices are increasingly adopted, such as improved irrigation techniques, integrated pest management, and the use of renewable energy sources in processing facilities.
Economic Significance
The almond industry is a significant contributor to the economies of producing regions. In California, for instance, the almond industry supports thousands of jobs, from farm labor to processing and distribution. The export market for almonds is substantial, with major markets in Europe, Asia, and North America.
Innovations and Future Trends
Technological Advancements
Advancements in agricultural technology are shaping the future of almond production. Precision agriculture, utilizing data analytics and satellite imagery, helps optimize irrigation, fertilization, and pest control. Innovations in processing, such as automated sorting and packaging, increase efficiency and product quality.
Sustainable Practices
Sustainability is becoming a focal point in the almond industry. Research into drought-resistant almond varieties, water-efficient irrigation methods, and zero-waste processing is ongoing. Sustainable farming practices not only help reduce the environmental footprint but also appeal to environmentally conscious consumers.
Market Trends
The demand for almonds continues to grow, driven by their health benefits and versatility. Almonds are used in various products, from snacks to dairy alternatives like almond milk. The industry is also exploring new markets and product innovations, such as almond-based protein powders and energy bars.
The journey of almonds from orchard to consumer involves a series of intricate steps, each crucial for ensuring the quality and safety of the final product. The almond industry exemplifies the integration of traditional agricultural practices with modern technology and sustainability efforts. As demand for almonds grows, the industry continues to innovate and adapt, ensuring that it meets the needs of consumers while addressing environmental and economic challenges. The careful cultivation, meticulous processing, and strategic market positioning of almonds highlight their significance in the global food industry.
Advantage & disadvantages of almond packing?
Packaging almonds involves various methods and materials, each with its own set of advantages and disadvantages. Here’s a detailed look at these aspects:
Advantages of Almond Packaging
Preservation of Freshness and Quality:
Barrier Protection: High-quality packaging materials like vacuum-sealed bags or airtight containers protect almonds from air, moisture, and contaminants, preserving their freshness and quality.
Extended Shelf Life: Proper packaging can significantly extend the shelf life of almonds by preventing oxidation and rancidity.
Convenience and Portability:
Portion Control: Packaging in smaller, single-serving sizes makes it easy for consumers to manage portions, enhancing convenience.
Ease of Transport: Well-designed packaging makes almonds easy to transport without spillage or damage.
Branding and Marketing:
Aesthetic Appeal: Attractive packaging can draw consumer attention and influence purchasing decisions.
Information Display: Packaging provides a platform for displaying nutritional information, brand stories, and usage instructions, which can educate and attract customers.
Safety and Hygiene:
Tamper Evident: Packaging can include tamper-evident features, ensuring the product is safe and has not been compromised.
Reduced Contamination: Properly sealed packaging reduces the risk of contamination from external sources.
Disadvantages of Almond Packaging
Environmental Impact:
Plastic Waste: Many packaging materials, particularly plastics, contribute to environmental pollution and are not biodegradable.
Resource Intensive: The production and disposal of packaging materials require significant resources and energy, contributing to carbon emissions and environmental degradation.
Cost:
Increased Expenses: High-quality packaging can be expensive, affecting the overall cost of the product. This can lead to higher prices for consumers.
Production Costs: Investment in advanced packaging technology and materials can be costly for manufacturers.
Complexity and Waste:
Over-Packaging: Sometimes, products are over-packaged, leading to unnecessary waste and increased environmental burden.
Disposal Issues: Consumers might face challenges in properly disposing of or recycling packaging materials, especially if they are not eco-friendly.
Potential Health Risks:
Chemical Leaching: Certain packaging materials, particularly some plastics, can leach harmful chemicals into the food, posing health risks.
Contamination: If not properly sealed or stored, packaging can sometimes fail, leading to contamination of the almonds.
Conclusion
Choosing the right packaging for almonds involves balancing the benefits of preserving freshness, enhancing convenience, and promoting the product, against the drawbacks related to environmental impact, cost, and potential health risks. Innovations in sustainable packaging materials and methods are continually evolving to address some of these disadvantages, aiming to provide safer, more eco-friendly options.
Leave a Reply