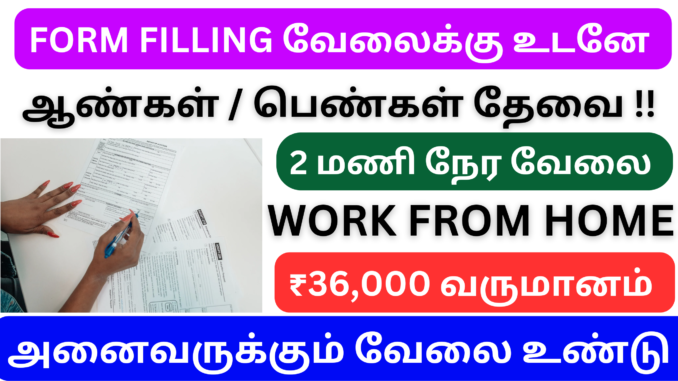
Form filling jobs / Work from home jobs tamil / Work from home / Part time jobs for students
Cardboard boxes making process :
The humble cardboard box, a ubiquitous item in our daily lives, is often overlooked despite its importance in packaging and transporting goods. However, the process of creating cardboard boxes is a fascinating journey involving several steps, from sourcing raw materials to the final product ready for use. In this essay, we will delve into the intricate process of making cardboard boxes, exploring each stage in detail.
Sourcing Raw Materials:
The journey of a cardboard box begins with the sourcing of raw materials. Cardboard, the primary material used, is made from wood pulp obtained from trees. The type of trees used varies depending on the desired quality of the cardboard. Softwood, such as pine and spruce, is commonly used due to its long fibers, which contribute to the strength of the cardboard.
Pulping:
Once the wood is harvested, it undergoes a pulping process where it is broken down into fibers. Pulping can be done using chemical, mechanical, or semi-chemical methods. Chemical pulping involves the use of chemicals to dissolve lignin, a natural adhesive in wood, leaving behind cellulose fibers. Mechanical pulping involves physically grinding or refining the wood to separate the fibers. Semi-chemical pulping combines elements of both chemical and mechanical methods.
Formation of Cardboard Sheets:
The next step involves forming the cardboard sheets. The pulp is mixed with water to create a slurry, which is then spread onto a wire mesh conveyor belt. As the water drains away, the fibers begin to bond together, forming a thin layer of wet cardboard. This layer is then pressed between rollers to remove excess water and improve the bonding of the fibers.
Drying and Conditioning:
Once the cardboard sheets are formed, they are fed through a series of heated rollers to dry them out completely. Drying is a critical step as it ensures that the cardboard sheets are free from moisture, which can weaken the material and affect the quality of the final product. After drying, the sheets may undergo conditioning to achieve specific properties such as smoothness or stiffness.
Corrugation:
Corrugated cardboard, commonly used in the manufacturing of boxes, consists of a fluted inner layer sandwiched between two flat outer layers. The process of corrugating involves passing the cardboard sheets through a series of corrugating rollers, which press a wave-like pattern into the middle layer. This corrugated layer adds strength and rigidity to the cardboard, making it ideal for packaging purposes.
Adhesive Application:
To bond the layers of corrugated cardboard together, adhesive is applied to the fluted layer. The type of adhesive used depends on various factors such as the intended application of the cardboard boxes and environmental considerations. Commonly used adhesives include starch-based adhesives, which are eco-friendly and water-soluble, and synthetic adhesives, which offer greater strength and durability.
Sheet Cutting and Creasing:
Once the adhesive has been applied, the corrugated cardboard sheets are cut to the desired size using precision cutting machines. These machines ensure uniformity in dimensions, crucial for the assembly of boxes. Additionally, creasing is done along the edges of the sheets to facilitate folding and forming of the boxes.
Printing and Finishing:
Printing is often applied to cardboard boxes to convey branding, product information, or decorative elements. This is typically done using flexographic or lithographic printing methods, which allow for high-quality printing on various surfaces. After printing, the cardboard boxes may undergo additional finishing processes such as laminating, coating, or embossing to enhance their appearance and durability.
Box Assembly:
The final step in the process involves folding and gluing the cardboard sheets to form the boxes. Automated assembly lines are often used for this purpose, where the cardboard sheets are fed through machines that fold, glue, and seal the boxes at high speeds. Quality control measures are implemented throughout the assembly process to ensure that the boxes meet the required standards.
Packaging and Distribution:
Once assembled, the cardboard boxes are ready to be filled with products and prepared for distribution. They play a crucial role in protecting goods during transportation and storage, ensuring that they reach their destination safely and intact. Cardboard boxes are lightweight, cost-effective, and recyclable, making them the preferred choice for packaging across various industries.
In conclusion, the process of making cardboard boxes is a complex yet efficient journey that involves multiple stages, from sourcing raw materials to the final assembly of the boxes.
Each step is carefully orchestrated to produce high-quality cardboard boxes that meet the diverse needs of modern packaging applications.
Despite their simple appearance, cardboard boxes play a vital role in our everyday lives, facilitating the movement of goods and contributing to the efficiency of global supply chains.
How to use Automatic cardboard making machine?
Using an automatic cardboard making machine typically involves several steps:
Setup: Ensure the machine is properly set up according to the manufacturer’s instructions. This includes connecting power, checking fluid levels if applicable, and making sure all safety features are in place.
Material Preparation: Prepare the cardboard material that will be used in the machine. This may involve loading rolls of cardboard into the machine or placing pre-cut sheets in the designated area.
Programming: If the machine is equipped with programmable settings, input the specifications for the cardboard you want to produce. This may include dimensions, thickness, and any additional features such as scoring or perforation.
Testing: Before running a full production cycle, it’s often a good idea to run a test to ensure everything is functioning correctly. This involves running a small batch of cardboard through the machine and inspecting the quality of the output.
Production: Once the machine is set up and tested, you can begin the production run. Depending on the machine’s capabilities, this may involve loading material, starting the machine, and monitoring the process to ensure smooth operation.
Quality Control: Throughout the production run, periodically inspect the quality of the cardboard being produced. Look for any defects or inconsistencies and make adjustments to the machine as needed.
Maintenance: After the production run is complete, perform any necessary maintenance tasks to keep the machine in good working condition. This may include cleaning, lubricating moving parts, and replacing worn components.
Shutdown: When you’re finished using the machine, shut it down according to the manufacturer’s instructions. This may involve powering off the machine, draining fluids if necessary, and securing any moving parts.
Always refer to the specific instructions provided by the manufacturer of your automatic cardboard making machine for detailed guidance on its operation and maintenance. Additionally, proper training and safety precautions should be followed to ensure safe operation of the equipment.
What is the purpose of used in cardboard box making?
The purpose of glue in cardboard box making is to bond the different parts of the box together, such as the flaps, panels, and seams.
It provides strength and structural integrity to the box, ensuring that it can hold its shape and withstand handling and shipping.
Glue also helps to seal the edges of the box, preventing contents from spilling out and protecting them from damage during transit.
Advantage & disadvantages of cardboard packing?
Cardboard packing, like any packaging material, comes with its own set of advantages and disadvantages:
Advantages:
Cost-effective: Cardboard is generally inexpensive compared to other packaging materials like plastic or metal.
Lightweight: It is lightweight, which reduces shipping costs and makes handling easier.
Versatile: Cardboard can be easily cut, folded, and shaped to accommodate various product shapes and sizes.
Recyclable: Cardboard is recyclable and biodegradable, making it an environmentally friendly option.
Customizable: It can be printed with logos, product information, and branding, enhancing product visibility and marketing.
Shock absorption: Cardboard provides a certain level of cushioning and protection to the packaged items.
Disadvantages:
Susceptible to moisture: Cardboard can be damaged by moisture, reducing its durability and protective qualities.
Not suitable for heavy items: While cardboard is lightweight, it may not be suitable for packaging heavy or bulky items as it lacks the strength and durability of materials like plastic or metal.
Limited durability: Cardboard packaging may not withstand rough handling or multiple uses as well as more durable materials.
Biodegradability concerns: While cardboard is biodegradable, its production can still have environmental impacts, especially if it involves deforestation or excessive energy consumption.
Limited protection: While it provides some cushioning, cardboard may not offer sufficient protection against impacts or rough handling, especially for fragile or delicate items.
Space-consuming: Cardboard packaging may take up more space compared to more compact packaging materials, which can increase storage and transportation costs.
Overall, cardboard packaging is a popular choice for many products due to its affordability, versatility, and eco-friendliness, but its suitability depends on the specific needs of the product and the shipping conditions.
Leave a Reply