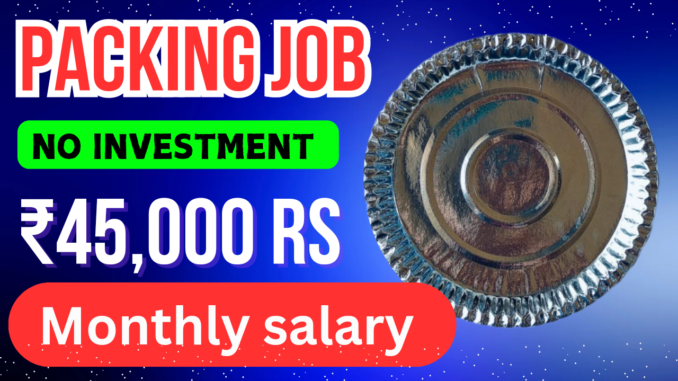
Packing jobs at home / Packing business at home / Best packing jobs 2024 / Part time jobs for students
paper plate manufacturing process :
Paper Plate Manufacturing Process
The manufacturing of paper plates is a systematic process that involves several stages, from raw material preparation to the final product. Paper plates are widely used due to their convenience, affordability, and eco-friendliness, making them a popular choice for events, parties, and food service. This comprehensive overview will break down the manufacturing process into key stages.
1. Raw Material Selection
The primary raw materials for paper plate production are:
Paper: Typically made from wood pulp, recycled paper, or a combination of both. The quality of the paper impacts the strength and durability of the plates.
Coatings: Some plates are coated with a thin layer of polyethylene or other materials to enhance grease resistance and waterproofing.
2. Pulping Process
The first step in creating paper for plates is pulping. This process converts raw materials into a slurry of fibers. There are two main methods of pulping:
Mechanical Pulping: Involves grinding wood logs to separate the fibers. This method retains most of the lignin, which can make the paper less durable.
Chemical Pulping: Uses chemicals to dissolve lignin and separate the fibers, resulting in stronger, higher-quality pulp. Common chemicals used include sodium hydroxide and sodium sulfide.
Once the pulp is prepared, it is washed and screened to remove impurities.
3. Sheet Formation
The next step is to convert the pulp into sheets of paper. This is done using a paper machine, which consists of several components:
Headbox: Distributes the slurry evenly onto the wire mesh.
Wire Section: Allows water to drain from the slurry, forming a wet sheet.
Press Section: Further removes water and compresses the sheet.
Drying Section: Uses heated rollers to dry the sheet completely.
The result is a continuous sheet of paper that can be cut to size for plate production.
4. Cutting and Die-Cutting
Once the paper sheets are ready, they are cut into specific sizes suitable for plates. This is typically done using a die-cutting machine. The process involves:
Feeding: Large rolls or sheets of paper are fed into the die-cutting machine.
Die-Cutting: A sharp die presses down on the paper, cutting it into circular or other shapes as required. The waste paper generated during this process is often recycled.
5. Forming the Plates
After cutting, the flat circles of paper need to be formed into plates. This is accomplished using a plate-forming machine, which typically involves:
Heating: The cut paper circles are heated to make them pliable.
Molding: The heated circles are placed into a mold that shapes them into the desired plate form. The machine often uses pressure to ensure that the paper conforms to the mold shape.
6. Coating (Optional)
For certain types of paper plates, a coating is applied to enhance their functionality. The coating process involves:
Polyethylene Coating: A thin layer of polyethylene is applied to make the plates moisture and grease-resistant. This is essential for plates intended for food service.
Other Coatings: Alternative coatings may be used depending on the desired properties, such as compostable materials for eco-friendly plates.
7. Quality Control
Quality control is a critical step in the manufacturing process. Each batch of paper plates undergoes several tests, including:
Strength Testing: Ensuring the plates can hold food without bending or breaking.
Coating Integrity: Checking for uniform application of coatings and resistance to moisture and grease.
Size and Shape Accuracy: Verifying that the plates meet specified dimensions and shapes.
8. Packaging
Once the plates pass quality control, they are ready for packaging. This process involves:
Counting: Plates are stacked and counted into predetermined quantities.
Wrapping: The plates are wrapped in plastic or placed into boxes to protect them during transportation and storage.
Labeling: Each package is labeled with essential information, including the number of plates, size, and any special features (e.g., biodegradable, compostable).
9. Distribution
After packaging, the final step is distribution. The packaged paper plates are transported to warehouses or directly to retailers and food service providers. Efficient logistics ensure that the product reaches the market in a timely manner.
The paper plate manufacturing process is a blend of traditional paper-making techniques and modern machinery, resulting in a product that is both functional and versatile. The use of eco-friendly materials and coatings reflects a growing awareness of sustainability in manufacturing practices.
As consumer demand for convenience and environmentally responsible products continues to rise, the paper plate industry is likely to evolve, adopting new technologies and materials to meet these changing needs.
How to pack paper plates :
Packing paper plates efficiently involves a few key steps to ensure they remain undamaged and organized. Here’s a comprehensive guide on how to do it:
Materials Needed
Paper Plates: Ensure they are clean and dry.
Box or Container: Choose a sturdy box that can accommodate the plates.
Packing Material: Bubble wrap, packing paper, or cardboard dividers to prevent shifting.
Tape: Strong packing tape to seal the box securely.
Markers: For labeling the box.
Plastic Wrap or Bags (optional): For extra protection.
Step-by-Step Packing Process
1. Preparation
Clean Work Area: Ensure your packing area is clear of clutter to avoid accidents.
Check the Plates: Inspect each plate for any damage or dirt. It’s essential to pack only usable plates to avoid any hygiene issues.
2. Choose the Right Box
Size Matters: Select a box that’s slightly larger than the stack of plates but not so large that the plates will shift around. A box that fits the plates snugly will offer better protection.
Strength of the Box: Use a double-walled cardboard box if you have a large quantity, as it provides additional strength.
3. Stack the Plates
Vertical vs. Horizontal: Decide if you want to pack the plates vertically or horizontally. Horizontal stacking is usually safer as it distributes weight evenly.
Align Plates: If stacking horizontally, place a few sheets of packing paper or cardboard between each layer to prevent sticking.
4. Use Packing Material
Cushioning: Place a layer of packing material at the bottom of the box. This will act as a cushion when the box is moved.
Fill Gaps: After stacking the plates, fill any gaps with packing material to prevent movement during transit.
5. Seal the Box
Close the Box: Once the plates are stacked and secured, close the box flaps.
Tape Securely: Use packing tape to seal the box securely. Ensure you tape all seams and edges to reinforce the structure.
6. Label the Box
Clear Labeling: Use a marker to label the box with contents, handling instructions (e.g., “Fragile” or “This Side Up”), and your name or destination if necessary.
Date the Box: If you’re packing multiple boxes, date them to keep track of when they were packed.
Additional Tips
Avoid Overpacking: Don’t overfill the box, as this can cause stress on the plates and lead to breakage.
Consider Weight: If you have a large number of plates, consider splitting them into multiple boxes to make them easier to handle.
Temperature Considerations: If the plates are made from eco-friendly materials, be aware of temperature changes during transit that might affect their integrity.
Unpacking
When you arrive at your destination:
Inspect the Plates: Check for any damage that may have occurred during transit.
Store Properly: Store the plates in a dry, cool place away from direct sunlight to maintain their quality.
Organize: Arrange the plates in a manner that makes them easy to access, perhaps in a stack or using a dedicated shelf.
Conclusion
Packing paper plates might seem straightforward, but taking the time to do it properly can save you from potential frustration and waste. By using the right materials and techniques, you can ensure your plates arrive safely and are ready for use. This method can be applied to other similar items, making it a useful skill for various packing needs.
By following these guidelines, you can efficiently pack paper plates and keep them safe for any event or occasion.
Leave a Reply