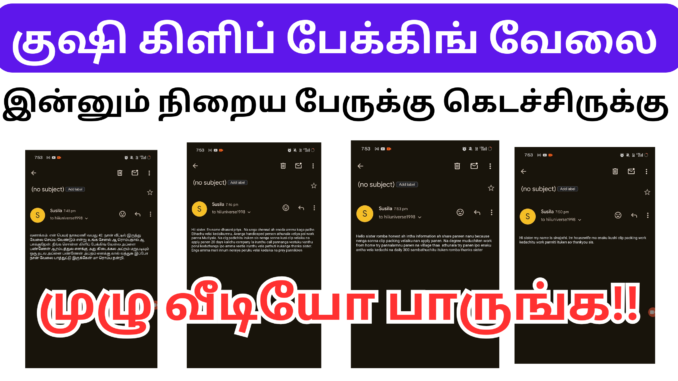
Packing jobs from home / Work from home / Home based jobs tamil / How to earn money online tamil
How to work packing jobs :
To create a 1000-word piece about packing jobs, you’ll want to cover a few key areas. Here’s a structured approach to help you write it:
Introduction (100-150 words):
Start with a brief introduction to packing jobs. Define what packing jobs are and why they are important. Highlight their role in various industries such as retail, manufacturing, logistics, and e-commerce.
Example:
Packing jobs are crucial roles in the logistics and retail sectors, ensuring that products are carefully packed, shipped, and delivered to customers. These positions are essential for maintaining inventory flow, preventing damage, and ensuring customer satisfaction. In this article, we’ll explore the responsibilities, skills, and benefits associated with packing jobs, as well as the challenges and opportunities they present.
Types of Packing Jobs (200-250 words):
Discuss the different types of packing jobs and where they can be found. Include examples such as:
Retail Packing: Packing items for online orders in e-commerce settings.
Industrial Packing: Packing products in manufacturing settings, often involving bulk items.
Specialty Packing: Packing delicate or high-value items, such as electronics or fragile goods.
Example:
Packing jobs can vary widely depending on the industry. In retail, packing roles involve preparing online orders for shipment, ensuring items are securely packed to prevent damage during transit. Industrial packing might involve handling larger quantities of products, often requiring more robust packing materials and techniques. Specialty packing, on the other hand, focuses on high-value or delicate items, where precision and care are paramount to prevent damage.
Key Responsibilities and Skills (250-300 words):
Outline the primary duties of packing jobs and the skills needed to perform them effectively.
Responsibilities:
Inspecting products for quality.
Selecting appropriate packing materials.
Packing items securely and efficiently.
Labeling and sorting packages.
Ensuring compliance with safety and regulatory standards.
Skills:
Attention to detail.
Physical stamina and dexterity.
Time management.
Basic math skills for measurements and calculations.
Familiarity with packing equipment and technology.
Example:
Packing jobs require a range of skills and responsibilities. Employees must inspect items for quality, select suitable packing materials, and pack products securely to avoid damage. Attention to detail is crucial, as is the ability to work quickly and efficiently. Physical stamina is often needed, as packing can involve repetitive tasks and lifting. Basic math skills are useful for measurements, and familiarity with packing technology can streamline the process.
Benefits and Challenges (200-250 words):
Describe the benefits and challenges of working in packing jobs. Include aspects such as job stability, opportunities for advancement, and physical demands.
Benefits:
Job Stability: Packing jobs are often in demand across various industries.
Skill Development: Workers can develop valuable skills that are transferable to other roles.
Opportunities for Advancement: With experience, there may be opportunities to move into supervisory or management roles.
Challenges:
Physical Demands: Packing can be physically demanding and repetitive.
Work Environment: Jobs may involve working in fast-paced or noisy environments.
Seasonal Fluctuations: Some packing jobs may be subject to seasonal demands, affecting job stability.
Example:
Packing jobs offer several benefits, such as job stability and opportunities for skill development. Workers can gain experience that is applicable in various fields and may find opportunities to advance into higher-level positions. However, these roles also come with challenges. The physical demands can be significant, involving repetitive tasks and potential strain. Additionally, the work environment might be fast-paced and noisy, and some positions may experience fluctuations in demand depending on the season.
Conclusion (100-150 words):
Wrap up by summarizing the importance of packing jobs and reflecting on the future outlook. Mention any emerging trends or changes in the industry that could impact packing roles.
Example:
Packing jobs play a vital role in ensuring that products reach customers safely and efficiently. As e-commerce continues to grow and technology advances, packing roles are evolving, with increased automation and sophisticated packing solutions. While packing jobs can be physically demanding, they offer stability and opportunities for growth. As the industry adapts to new trends, those in packing roles may find new opportunities to develop their skills and advance their careers.
Peanuts making process :
Sure, here’s a detailed overview of the peanut processing journey:
The Journey of Peanuts: From Farm to Table
Peanuts, also known as groundnuts, undergo a fascinating transformation from a humble legume growing underground to a popular snack or ingredient in various foods. The process of peanut production and processing involves several stages, each critical to ensuring the quality and safety of the final product.
1. Cultivation and Harvesting
Planting: Peanuts are typically planted in well-drained, sandy loam soils with a pH between 5.9 and 7.0. The seeds are sown in rows about 30 inches apart and 1.5 to 2 inches deep. Peanuts thrive in warm climates and are usually planted in the spring after the last frost. The plants grow to about 18 to 24 inches tall and produce yellow flowers that, once pollinated, develop into pegs that grow underground.
Growing: Peanuts require a growing season of about 120 to 150 days, depending on the variety. The plants need adequate water, particularly during the pegging and pod development stages, but excessive moisture can lead to fungal diseases. Proper weed and pest management is crucial to prevent competition and damage to the plants.
Harvesting: Peanuts are harvested when the leaves turn yellow, and the pods have matured. Harvesting usually occurs in late summer or early fall. Specialized machinery, known as peanut diggers, are used to lift the plants from the soil. These machines also shake the soil off the roots and turn the plants upside down to allow the peanuts to cure in the field for several days. This curing process helps reduce the moisture content and prepares the peanuts for drying.
2. Drying and In-Shell Processing
Drying: After harvesting, peanuts need to be thoroughly dried to a moisture content of about 10-12% to prevent mold growth and spoilage. They are spread out in drying bins or placed in drying facilities where air circulation helps to reduce moisture levels. Proper drying is essential to ensure the peanuts remain in good condition throughout processing.
In-Shell Processing: In-shell peanuts are then processed to remove debris and separate good-quality nuts. They go through cleaning machines that use air and screens to remove dirt, leaves, and other contaminants. The cleaned peanuts are sorted by size and weight, and any damaged or diseased nuts are removed.
3. Shelling and Sorting
Shelling: The next stage is shelling, where the outer shells of the peanuts are removed to reveal the edible kernels. Modern shelling machines can efficiently separate the shells from the nuts. These machines use a combination of mechanical force and vibration to crack the shells and remove the kernels. The shell fragments are then collected for use as animal feed or compost.
Sorting: Once shelled, peanuts are sorted to ensure uniform quality. They are passed through a series of screens and air blowers to remove any remaining shell fragments, broken pieces, and foreign materials. Peanuts are then graded based on size, color, and any defects. Automated sorting systems, including optical sorters, use cameras and sensors to identify and remove defective peanuts.
4. Blanching and Roasting
Blanching: Blanching is a process used to remove the skin of the peanut kernels. Blanching machines steam the peanuts to loosen the skins, which are then removed mechanically. This step is often performed for peanuts intended for use in products like peanut butter or as ingredients in baked goods.
Roasting: Roasting is a key step that enhances the flavor and texture of peanuts. Raw peanuts are roasted in large, rotating drums or in hot air roasters at temperatures ranging from 320°F to 350°F (160°C to 175°C) for about 10-20 minutes. The roasting process also helps in developing the characteristic aroma and crunchiness of peanuts. After roasting, peanuts are cooled quickly to stop the cooking process and preserve their flavor.
5. Grinding and Processing
Grinding: For products like peanut butter, roasted peanuts are ground into a paste. The grinding process can be adjusted to produce different textures, from smooth to chunky. Peanuts are fed into grinders that crush and blend them, creating a consistent paste. In some cases, additional ingredients like salt, sugar, or oils are added to enhance flavor and texture.
Processing: Beyond peanut butter, peanuts are also processed into various products such as peanut oil, peanut flour, and snack items. Peanut oil is extracted through pressing or solvent extraction, and peanut flour is made by grinding roasted peanuts and removing the oil. Each product requires specific processing techniques to achieve the desired quality and characteristics.
6. Packaging and Distribution
Packaging: After processing, peanuts and peanut products are packaged for distribution. Packaging helps to protect the products from contamination and spoilage. For in-shell peanuts, the packaging might involve bulk containers or retail-sized bags. Peanut butter and other processed products are packaged in jars, cans, or pouches, depending on the intended market.
Distribution: Once packaged, peanuts and peanut products are distributed to retailers, food manufacturers, and other customers. Distribution involves logistics to ensure the products reach their destinations efficiently and in good condition. This might include warehousing, transportation, and inventory management.
7. Quality Control and Safety
Throughout the entire processing chain, rigorous quality control measures are in place to ensure the safety and quality of peanuts. This includes checking for contaminants, monitoring moisture levels, and ensuring compliance with food safety standards. Regular inspections and testing are conducted to detect any potential issues and ensure that the final products meet industry regulations.
In summary, the process of turning peanuts from their natural state into a consumer-ready product involves careful cultivation, harvesting, drying, shelling, roasting, and processing. Each step is crucial to preserving the quality and safety of the peanuts, ultimately delivering a nutritious and delicious product to consumers around the world.
Leave a Reply