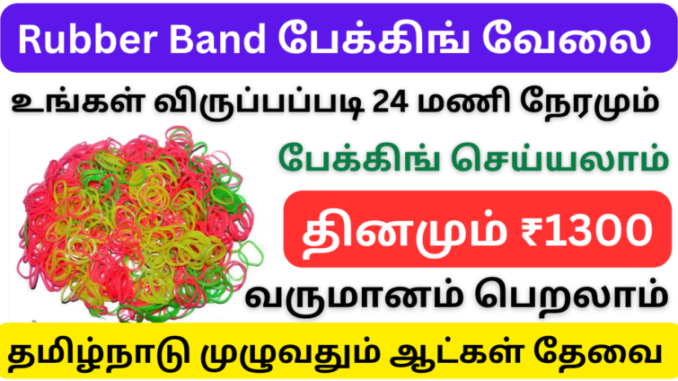
Home based packing jobs tamil 2023 / Best packing jobs from home / Packing business at home / Packing jobs at home tamil
Home based Rubber band packing
Rubber band packing, also known as rubber band ball packing, is a unique and creative way to package items using rubber bands.
It involves wrapping rubber bands around an item or a group of items until they form a tight ball or bundle, which provides protection, organization, and an aesthetic appeal.
Rubber band packing has gained popularity in recent years due to its eco-friendly and sustainable nature, as well as its versatility and practicality in various packing scenarios.
The process of rubber band packing begins with selecting the appropriate size and type of rubber bands.
Rubber bands come in various sizes, colors, and materials, such as natural rubber, silicone, or synthetic rubber.
The choice of rubber bands depends on the size and weight of the items being packed, as well as the desired level of tension and elasticity.
Thicker and wider rubber bands are suitable for larger and heavier items, while thinner and narrower bands work well for smaller and lighter items.
The color of the rubber bands can be chosen for aesthetic purposes or for easy identification of the packed items.
Once the rubber bands are selected, the packing process begins. The first step is to wrap a rubber band around the item or items being packed, securing it tightly with a simple twist.
Additional rubber bands are then wrapped around the item in a crisscross or spiral pattern, creating multiple layers of rubber bands that interlock and hold the items securely in place.
The tension of the rubber bands can be adjusted by stretching them more or less, depending on the level of tightness desired for the packing.
As the rubber bands are added, the item or items being packed gradually form a ball or a bundle, with the rubber bands tightly wound around them.
The rubber bands distribute the pressure evenly, protecting the packed items from scratches, dents, and other forms of damage during transit or storage.
The rubber bands also create a flexible and resilient packing solution that can absorb shocks and impacts, making it suitable for fragile or delicate items.
Rubber band packing offers several advantages over traditional packing methods. One of the key benefits is its eco friendliness and sustainability.
Rubber bands are typically made from renewable and biodegradable materials, such as natural rubber or silicone, which are more environmentally friendly than plastic or other synthetic materials commonly used in packing.
Rubber bands are also reusable, which reduces the amount of waste generated from packing materials.
Rubber band packing promotes a zero waste approach to packing, as the rubber bands can be easily removed and reused for other packing purposes, or recycled to minimize their environmental impact.
Another advantage of rubber band packing is its versatility and adaptability to various packing scenarios.
Rubber bands can be used to pack a wide range of items, from small household objects like pens, pencils, and keys, to larger items like books, clothes, and electronics.
Rubber band packing is suitable for packing irregularly shaped items or items with odd dimensions, as the flexibility of rubber bands allows them to conform to the shape of the items being packed.
Rubber band packing can also be used for organizing and bundling items together, making it a practical solution for keeping items tidy and easily accessible.
Rubber band packing also offers an aesthetic appeal that can enhance the visual presentation of the packed items.
The colorful and textured appearance of rubber bands can create an attractive and eye-catching packing solution, which can be particularly appealing for gift wrapping or for showcasing products in a retail setting.
Rubber band packing allows for creativity and customisation , as different colors, patterns, and tension levels of rubber bands can be combined to create unique and personalized packing designs.
In addition to its environmental benefits and aesthetic appeal, rubber band packing also provides practical advantages in terms of efficiency and cost-effectiveness.
Rubber bands are readily available and affordable, making them a cost-effective packing option compared to other packing materials. Rubber band packing can also be a time saving option
How to make rubber bands in industry :
Rubber bands are an essential and ubiquitous item used in a wide range of applications, from securing bundles of papers to industrial and agricultural uses.
They are widely used in various industries, such as packaging, printing, agriculture, logistics, and more.
The production of rubber bands is a complex and highly automated process that involves several stages, including material selection, mixing, extrusion, curing, cutting, and packaging.
In this article, we will delve into the process of making rubber bands in the industry in detail, covering the various steps involved and the materials used.
Material Selection:
The first step in making rubber bands is selecting the right materials. Rubber bands are typically made from natural rubber or synthetic rubber, such as polyisoprene, which is a polymer derived from petroleum.
Natural rubber is obtained from the latex of rubber trees, while synthetic rubber is manufactured from chemical compounds.
The choice of material depends on the desired characteristics of the rubber band, such as elasticity, durability, and strength.
Mixing:
Once the rubber material is selected, it is mixed with various additives to create a compound with the desired properties.
These additives may include accelerators, antioxidants, curing agents, and fillers. The compound is mixed in a large machine called a Banbury mixer, which blends the rubber and additives together to create a homogenous mixture.
The mixing process is carefully controlled to ensure that the ingredients are evenly distributed throughout the compound.
Extrusion:
After the rubber compound is mixed, it is fed into an extruder, which is a machine that shapes the compound into a continuous strip or tube.
The extruder consists of a barrel with a screw inside that moves the rubber compound forward as it melts due to heat and pressure.
The heat and pressure cause the rubber to become soft and pliable, allowing it to be shaped into the desired form. The extruded rubber strip or tube is then cooled using water or air to solidify it.
Curing:
Once the extruded rubber has cooled and solidified, it is subjected to a curing process to transform it from a soft, pliable material into a resilient and elastic rubber band.
Curing is typically done through a process called vulcanisation , which involves heating the rubber to a specific temperature and time, while also adding a curing agent.
The curing agent reacts with the rubber to create chemical bonds, which cross-link the polymer chains and make the rubber more rigid and durable.
The exact curing process may vary depending on the type of rubber and the desired properties of the final rubber bands.
Cutting:
After the curing process, the rubber strip or tube is cut into individual rubber bands of the desired length.
This is typically done using cutting machines that are programmed to cut the rubber bands to specific lengths.
The cut rubber bands are then inspected for quality, including checking for any defects or inconsistencies.
Packaging:
Once the rubber bands are cut and inspected, they are packaged for distribution. Packaging may involve various methods, such as bundling the rubber bands together using plastic or paper, or placing them in containers or bags.
The packaging is designed to protect the rubber bands from damage during transportation and storage and to provide convenience for users.
Quality Control:
Throughout the entire production process, quality control measures are implemented to ensure that the rubber bands meet the required standards.
This may involve conducting tests on the raw materials, monitoring the mixing process, inspecting the extruded rubber, conducting curing tests, and checking the cut rubber bands for defects.
Any rubber bands that do not meet the quality standards are rejected and not packaged for distribution.
Automation:
The production of rubber bands in the industry is largely automated, with sophisticated machinery and equipment used at various stages of the process.
Automation allows for high production volumes, increased efficiency, and consistent quality.
Benefits of rubber band packing?
Rubber band packing, also known as banding or bundling, involves using rubber bands to secure and hold together items or materials for various purposes. Here are some benefits of rubber band packing:
Cost-effective: Rubber bands are relatively inexpensive compared to other types of packaging materials such as tapes, plastic wraps, or adhesives, making them a cost-effective option for bundling and securing items.
Versatility: Rubber bands come in various sizes, shapes, and strengths, making them versatile for different packing needs. They can be used to bundle a wide range of items, including papers, envelopes, pens, pencils, cutlery, tools, cables, and many other objects.
Ease of use: Rubber bands are easy to apply and remove, making them convenient for packing and unpacking tasks. They can be quickly stretched over items and provide a firm grip without requiring any special tools or equipment.
Flexibility: Rubber bands are flexible and stretchable, allowing them to accommodate items of different sizes and shapes. They can expand and contract to fit tightly around items, providing a secure hold and minimizing the risk of items shifting or moving during transit.
Reusability: Rubber bands can be reused multiple times, reducing the need for additional packing materials and contributing to sustainability efforts. They can be easily removed and reused for other packing tasks, making them an environmentally-friendly packing option.
Protection: Rubber bands can provide a gentle yet firm grip on items without causing damage or leaving residue. They can hold items together without scratching, denting, or marking the surfaces, making them ideal for packing delicate or sensitive items.
Time saving: Rubber band packing can be a time saving option compared to other packaging methods that require additional steps, such as cutting tapes or applying adhesives. Rubber bands can be quickly stretched over items, saving time and effort in the packing process.
Overall, rubber band packing offers several benefits, including cost-effectiveness, versatility, ease of use, flexibility, reusability, protection, and time saving , making it a popular choice for bundling and securing items in various settings.
Leave a Reply