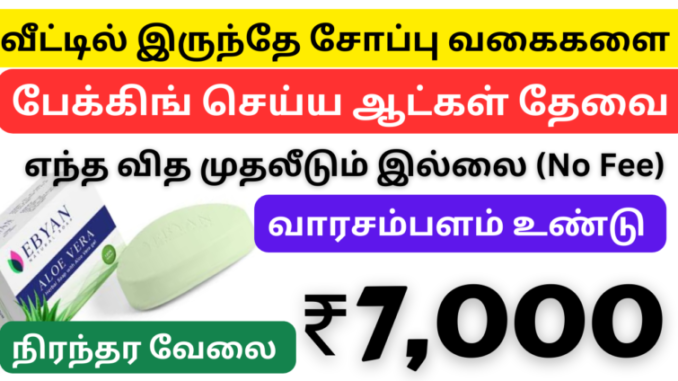
Home based packing jobs tamil / Part time jobs for students / Best part time job / Home based packing jobs 2023
Bath soap manufacturing methods
Bath soap is a cleansing agent that is used to remove dirt, oil, and impurities from the skin. It is made from a combination of fats, oils, and alkaline solutions.
The process of making soap has been around for thousands of years and has evolved over time to become more efficient and effective.
There are several methods for manufacturing soap, each with its own advantages and disadvantages. In this article, we will explore the most commonly used methods of bath soap manufacturing.
Cold Process Method
The cold process method is the most traditional method of soap making. It involves mixing oils or fats with a strong alkali solution, typically sodium hydroxide or lye.
The mixture is then stirred until it thickens and solidifies. This process can take several hours or even days.
The main advantage of this method is that it allows for a lot of creativity in terms of the ingredients used. Soap makers can add various oils, fragrances, and colors to create unique and personalized soaps.
However, the process can be time-consuming and requires careful attention to detail to ensure the correct ratios of ingredients are used.
Hot Process Method
The hot process method is similar to the cold process method, but with the addition of heat. The oils and lye solution are combined and then heated in a pot or crock pot until the mixture reaches the desired consistency.
This method typically takes less time than the cold process method, as the heat speeds up the saponification process.
One advantage of this method is that it produces a harder bar of soap that lasts longer than soap made using the cold process method. However, it can be more difficult to achieve a smooth and consistent texture with the hot process method.
Melt and Pour Method
The melt and pour method is the easiest and quickest way to make soap. It involves melting pre-made soap bases, which typically contain a combination of oils, lye, and other ingredients, and then pouring them into moles.
This method is popular among hobbyists and beginners because it requires little skill or knowledge.
The main advantage of this method is its simplicity and convenience. Soap makers can create a variety of soaps quickly and easily without the need for complex equipment or specialized ingredients.
However, this method can be limiting in terms of creativity, as soap makers are limited to the pre-made soap bases and cannot control the ingredients used.
Re batching Method
The re batching method, also known as the hand milled method, involves taking pre-made soap bars and melting them down to create new soap bars.
This method is popular among soap makers who want to recycle old soap scraps or create unique soap blends.
The main advantage of this method is that it allows for creative freedom and the ability to use up old soap scraps. However, the process can be time-consuming and requires careful attention to detail to ensure the correct ratios of ingredients are used.
Liquid Soap Method
The liquid soap method involves using potassium hydroxide instead of sodium hydroxide as the alkali solution. This method produces a liquid soap rather than a solid bar.
The process involves combining oils and potassium hydroxide in a pot and then heating the mixture until it thickens into a liquid soap.
One advantage of this method is that it produces a soap that is easier to use in a pump bottle or dispenser.
Additionally, liquid soap can be used for a variety of purposes, including hand soap, body wash, and shampoo. However, the process can be more difficult than other methods and requires precise measurements to ensure the correct ratios of ingredients are used.
In there are several methods for manufacturing bath soap, each with its own advantages and disadvantages. The cold process, hot process, melt and pour, re batching, and liquid soap methods are the most commonly used.
How to pack bath soaps in industry?
The process of packing bath soaps in an industry typically involves the following steps:
Soap Cutting: The soap blocks are first cut into smaller pieces of a desired size and shape using specialized machines.
Wrapping: The individual soap bars are then wrapped in either plastic film or paper, depending on the desired packaging.
Labeling: Once the soap bars are wrapped, they are labelled with the appropriate product information such as the brand name, ingredients, and manufacturing date.
Boxing: The wrapped and labelled soap bars are then packed into boxes in the desired quantity for shipment.
Quality Control: Throughout the packing process, quality control checks are performed to ensure that the soap bars meet the industry’s standards for appearance, scent, and consistency.
Overall, the process of packing bath soaps in an industry requires specialized machinery and skilled workers to ensure that the soap bars are packaged properly and meet the industry’s high standards for quality.
Benifits of soap manufacturing
Soap manufacturing offers several benefits, both for individuals and society as a whole. Here are some of the key benefits:
Improved hygiene: Soap is an essential personal hygiene product that helps to remove dirt, oil, and bacteria from the skin. Regular use of soap can help prevent the spread of diseases and infections.
Employment opportunities: Soap manufacturing creates jobs, both directly and indirectly. This includes jobs in production, packaging, marketing, and distribution.
Economic development: Soap manufacturing can contribute to the growth of the economy, as it generates income for manufacturers, suppliers, and retailers. This income can then be reinvested into the local economy, creating a positive ripple effect.
Sustainable production: Many soap manufacturers are committed to using sustainable production methods, such as using natural ingredients and reducing waste. This can help to reduce the environmental impact of soap production.
Personalization of products: Soap manufacturing allows for a wide range of customisation , from the type of ingredients used to the packaging and branding. This can create a unique and personalized product that meets the needs and preferences of different customers.
Overall, soap manufacturing offers a range of benefits that go beyond personal hygiene. From job creation to economic development, soap manufacturing can have a positive impact on individuals and society as a whole.
Advantage & disadvantages of bath soap manufacturing
Advantages of Bath Soap Manufacturing:
High Demand: Soap is a daily-use product that has a high demand in the market. Thus, it has a stable and growing market, providing steady revenue to the manufacturers.
Customisation : Manufacturers can customize soaps based on the different needs of consumers such as skin type, fragrance preferences, etc.
Profit Margins: The production cost of soap is relatively low compared to the selling price, which allows for higher profit margins.
Large Scale Production: Bath soap manufacturing can be done on a large scale, making it easier for manufacturers to meet the high demand and provide economies of scale.
Multiple Sales Channels: Soap can be sold through multiple sales channels like supermarkets, online stores, and direct sales, providing a wider reach to consumers.
Disadvantages of Bath Soap Manufacturing:
Competition: The soap manufacturing industry is highly competitive, making it challenging for new manufacturers to establish themselves in the market.
Environmental Concerns: Soap production can cause environmental concerns as it generates a significant amount of wastewater, and the packaging material used can also be harmful to the environment.
Health and Safety Concerns: Soap production involves the use of caustic chemicals that can be dangerous if not handled with care, and the working conditions in soap manufacturing units can also pose health and safety risks to the workers.
Cost of Production: Although the production cost of soap is relatively low, the initial investment required to set up a manufacturing unit can be high.
Quality Control: Maintaining quality standards and consistency in the production process can be a challenge, which can affect customer satisfaction and loyalty.
Leave a Reply